Worker Dies During Hot Work \ Welding
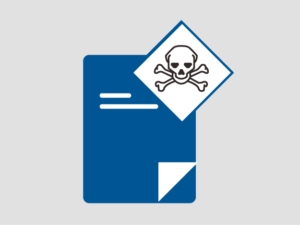
INCIDENT
In November 2011, two contractors at the E. I. DuPont De Nemours Co. located in Buffalo, New York, were performing welding atop a 10,000-gallon slurry tank when hot sparks ignited flammable vapors, causing an explosion that killed one contractor and seriously injured another. The CSB’s final report and safety video, entitled “Hot Work: Hidden Hazards,” were released at an April 19, 2012, public meeting. A primary cause of the blast was established by the CSB as the failure of the company to require that the interior of storage tanks—on which hot work was to be performed—be monitored for flammable vapor. The CSB issued a recommendation urging DuPont to require monitoring inside and around storage tanks prior to performing any hot work.
NEED TO KNOW
Hazards / Dangers
Hot work produces electrical arcs or flames that can reach up to 10,000. High temperatures, sparks and slag, are also an ever-present danger. Hot work equipment, such as arc welding circuits, can cause serious or fatal electrocution. Arc welding produces intense UV light that can damage welders’ retinas.
Health Dangers:
These components in welding smoke can affect the welder’s lungs, heart, kidneys and central nervous system. Long-term exposure to welding smoke can cause chronic respiratory problems, decreased lung capacity, heart disease, skin disease, hearing loss, kidney damage, reproductive harm, and other diseases.
As defined by NFPA 51B, hot work is any work that involves “burning, welding, or a similar operation that is capable of initiating fires or explosions.” It’s not just work that involves flames. After all, you don’t need a flame to generate heat. Activities such as drilling, soldering, brazing, tapping, grinding, heat treating, chipping, thawing pipes, and abrasive blasting—often referred to as sand blasting—are all considered hot work.
According to the NFPA report on hot work structure fires, soldering causes 34 percent of hot work fires started in homes. Because this work must usually be performed close to combustible construction materials and insulation, it can be a significant hot work safety challenge.
NFPA 51B and other hot work safety practices require someone—normally a trained fire watch—to remain at the work site for a minimum of 30 minutes after hot work has stopped to monitor the site for any smoldering conditions or reignition from hot embers or retained heat. And heat has a way of sticking around. Insurance data indicates that retained heat has contributed to reignition conditions up to four hours after the hot work was performed.
NFPA 51B requires establishing a hot work safety team consisting of three individuals: the person in charge (referred to in NFPA 51B as the permit authorizing individual, or PAI); a hot work operator; and a fire watch. The standard defines their duties as being responsible for safety on the work site and identifying any change in conditions so that hot work stops until the conditions are reevaluated. The message on the job site for all workers is if they see something that might be an unsafe change in condition, they need to tell someone so it can be checked.
Many types of hot work, such as welding, grinding, and torch cutting, produce sparks, slag, or spatter that can reach well beyond the immediate work area. For that reason, NFPA 51B establishes a minimum safe distance of 35 feet in all directions from the location of the hot work. In other words, combustible materials must be moved at least 35 feet away from the work to prevent contact with the hot work residue, such as sparks or slag. That distance is only a minimum, and conditions such as wind or proximity to dry grass might necessitate a greater distance. While working at an elevated location, for instance, where sparks can fall vertically.
BUSINESS / REGULATIONS
In February 2010, the U.S Chemical Safety and Hazard Investigation Board (CSB) released “Seven Key Lessons to Prevent Worker Deaths during Hot Work in and Around Tanks,” a safety bulletin that provided summaries and findings from 11 investigations. (It also notes that 60 fatalities occurred due to hot work between 1990 and 2010.) In addition, the bulletin provided seven key lessons aimed at preventing worker deaths during hot work in and around storage tanks containing flammable materials. These include:
- Use Alternatives:Whenever possible, avoid hot work and consider alternative methods.
- Analyze the Hazards:Prior to the initiation of hot work, perform a hazard assessment that identifies the scope of the work, potential hazards, and methods of hazard control.
- Monitor the Atmosphere:Conduct effective gas monitoring in the work area using a properly calibrated combustible gas detector prior to and during hot work activities, even in areas where a flammable atmosphere is not anticipated.
- Test the Area:In work areas where flammable liquids and gases are stored or handled, drain and/or purge all equipment and piping before hot work is conducted. When welding on or in the vicinity of storage tanks and other containers, properly test and, if necessary, continuously monitor all surrounding tanks or adjacent spaces—not just the tank or container being worked on—for the presence of flammables and eliminate potential sources of flammables.
- Use Written Permits:Ensure that qualified personnel familiar with the specific site hazards review and authorize all hot work and issue permits specifically identifying the work to be conducted and the required precautions.
- Train Thoroughly:Train personnel on hot work policies/procedures, proper use and calibration of combustible gas detectors, safety equipment, and job–specific hazards and controls in a language understood by the workforce.
- Supervise Contractors:Provide safety supervision for outside contractors conducting hot work. Inform contractors about site-specific hazards, including the presence of flammable materials.
Due to the frequency and severity of hot work accidents, the CSB has designated safe hot work practices as one of the five elements of its newly developed Drivers of Critical Chemical Safety Change Program. The CSB’s Drivers of Critical Chemical Safety Change are based on recommendations resulting from CSB investigations and studies. The goal of the program is to pursue implementation of changes most likely to achieve important national-level safety improvements.
The CSB has continued to advocate for best practices and recommended improvements of consensus standards, specifications, recommended practices, technical reports, and codes to address hot work activities. NFPA standards and codes referenced by the CSB in its hot work investigations include NFPA 51B, Fire Prevention During Welding, Cutting, and Other Hot Work; NFPA 326, Safeguarding of Tanks and Containers for Entry, Cleaning, or Repair; and NFPA 70E®, Electrical Safety in the Workplace®. In addition, the CSB has continued to push for the adoption of its recommendations aimed at preventing hot work incidents by emphasizing the need for increased hot work hazard awareness among workers and the need for stronger oversight and responsibility for hot work activities.
STATISTICS
Industrial Safety & Hygiene News, using figures from OSHA studies, reports that 1 in 250 construction workers will die from a welding injury. With over half a million American welders working today, we can conservatively expect 2,000 welding fatalities in our lifetime. That’s not even mentioning the many more permanent injuries that welders will incur.
- From 2001-2018, five firefighters were fatally injured in four unintentional fires started by torches.
The U.S. Chemical Safety and Hazard Investigation Board (CSB) has found that hot work is one of the most common causes of worker deaths among incidents investigated by the agency. The CSB continues to see hot work incidents and has found a significant subset of occurrences—those involving piping, tanks, or containers where flammables are present—to be particularly dangerous. In addition, the CSB repeatedly observes hot work incidents involving tanks or containers at high-hazard facilities such as refineries and chemical plants that typically result in injuries and fatalities and have the potential to result in major catastrophic accidents.
Since 2001, the CSB has deployed to and investigated 14 hot work–related incidents that have resulted in 25 fatalities and 21 injuries to employees and members of the public. The CSB continues to monitor hot work incidents where continuous monitoring could have alerted workers to the changing conditions in areas where hot work activity was conducted.
Between 2010 and 2013, the CSB reviewed 187 hot work incidents, 85 of which resulted in a fire or explosion while hot work was being conducted on or near a tank or container. These incidents resulted in 48 fatalities and 104 significant injuries. Twenty-three percent of injuries and 42 percent of fatalities involved contractor workers.
The CSB continues to see catastrophic incidents involving hot work on tanks and containers containing flammable vapors. Our past investigations into these incidents demonstrate a lack of awareness of the hazards of conducting hot work on containers that in some cases had previously been cleaned. The CSB recently deployed to two hot work incidents, one at the Sunoco Logistics LP terminal in Nederland, Texas, and the other at the PCA facility in DeRidder, Louisiana. At Sunoco, seven contractors were injured in a flash fire while conducting hot work on a pipeline on August 12, 2016. On February 8, 2017, three contractors were fatally injured in an explosion at the PCA facility while conducting hot work.
According to the NFPA report “Structure Fires Started by Hot Work,” issued last September, fire departments in the United States responded to an average of 4,400 structure fires a year involving hot work from 2010 to 2014.
There are other revealing statistics.
According to estimates from the Consumer Product Safety Commission (CPSC’s) National Electronic Injury Surveillance System (NEISS), and estimated 11,500 people visited hospital emergency departments because of injuries associated with welding soldering, and cutting tools considered consumer products in 2018.
Note that in many cases, no fire occurred.
- Radiation burns to the eyeball caused 4,300 (58%) of these injuries.
- 2,300 (20%) of the injuries involved foreign bodies in the eyes.
The following examples from the NEISS narratives show the importance of wearing eye protection
- A 25-year-old man who was welding without eye protection suffered radiation burns to his eyes.
- A 35-year-old female was assisting someone who was welding and later woke with “burning, itching, eye pain, and photophobia”. She was diagnosed with welder’s keratitis.
- Welding debris caused a corneal abrasion in a 69-year-old man.
- A 32-year-old man went to the ED after suffering flash burns while welding the night before.
- A 43-year-old man burned his eyes while welding without wearing eye protection.
- A 55-year-old man had a piece of metal in his eye. He believed that this occurred while soldering the night before.
- Foreign material fell into the eye of a 51-year-old man who was welding under a car.
CPSC estimates that another 1,800 (16%) of the injuries associated with welding, soldering, and cutting tools were thermal burns. Some of these were due to contact with hot metal or a blow torch; others involved actual fires.
- A 25-year-old man was welding at home when sparks ignited his jacket causing second-degree burns to his forearm.
- A 76-year-old man was welding when a spark ignited his pants causing burns to his lower leg.
- A 49-year-old man burned his hand on hot metal while welding.
- An 18-year-old man picked up a piece of bare metal while welding barehanded.
PREVENTION
Staying safe is encapsulated in the 4 following procedures.
- Hot work management program.
- Substitutes / Alternatives.
- Good Practices Checklist.
- Personal Protective Equipment.
These four aspects incorporate the basis of preventative and precautionary steps to protect workers from harm in this dangerous hot work undertakings.
- Hot Work Management Program
Hot work programs are designed to control or eliminate hot work hazards and their risks including policies, procedures, and the assignment of responsibilities for all aspects of hot work.
- Policies
- Where hot work is permitted.
- When hot work is permitted.
- Who authorizes, performs, and monitors hot work activities.
- Procedures
- What must be assessed before permitting/performing hot work in an area or on a process piece of equipment or area.
- What to do to prepare an area for hot work.
- What to do if hot work cannot be avoided in a particularly hazardous area.
- What hot work tools are required?
- How to obtain a hot work permit, when they are required, and who can administer them.
- Training
- Employees, supervisors, maintenance individuals, fire wardens, trained fire watch individuals, and contractors all have different roles, and must be trained accordingly.
- Communications
- Posting procedures.
- Posting policies.
- Posting signs in areas that are prohibited from having hot work performed in them.
- Substitutes / Alternatives
Assess the substitutes or alternate method for any risks or hazards. Do not introduce any new risks or hazards.
- Good Practices Checklist
- Make sure that all equipment is in good operating order before work starts.
- Make sure that all appropriate personal protective devices are available at the site and each worker has been trained on how to use, clean, and store them properly.
- Inspect the work area thoroughly before starting. Look for combustible materials in structures (partitions, walls, ceilings).
- Move all flammable and combustible materials away from the work area.
- If combustibles cannot be moved, cover them with fire resistant blankets or shields. Protect gas lines and equipment from falling sparks, hot materials, and objects.
- Sweep clean any combustible materials on floors around the work zone. Combustible floors must be kept wet with water or covered with fire resistant blankets or damp sand.
- Use water ONLY if electrical circuits have been de-energized to prevent electrical shock.
- Remove any spilled grease, oil, or other combustible liquid.
- Vacuum away combustible debris from inside ventilation or other service duct openings to prevent ignition. Seal any cracks in ducts. Prevent sparks from entering into the duct work. Cover duct openings with a fire-resistant barrier and inspect the ducts after work has concluded.
- Make sure that appropriate fire extinguishers (e.g., ABC fire extinguishers) are available and easily accessible.
- Make sure that the first-aid boxes are available and easily accessible.
- Block off cracks between floorboards, along baseboards and walls, and under door openings, with a fire-resistant material. Close doors and windows.
- Cover wall or ceiling surfaces with a fire resistant and heat insulating material to prevent ignition and accumulation of heat.
- Secure, isolate, and vent pressurized vessels, piping and equipment as needed before beginning hot work.
- Inspect the area following work to ensure that wall surfaces, studs, wires or dirt have not heated up.
- Post a trained fire watcher within the work area, including lower levels if sparks or slag may fall during welding, including during breaks, and for at least 60 minutes after work has stopped. Depending on the work done, the area may need to be monitored for longer (up to 3 or more hours) after the end of the hot work until fire hazards no longer exist.
- Eliminate explosive atmospheres (e.g., vapors or combustible dust) or do not allow hot work. Shut down any process that produces combustible atmospheres, and continuously monitor the area for accumulation of combustible gases before, during, and after hot work.
- If possible, schedule hot work during shutdown periods.
- Comply with the required legislation and standards applicable to your workplace.
- Personal Protective Equipment
Eye and face protection, such as goggles and face shield or helmets, helps protect workers from hot sparks and molten particles. Other common PPE for hot work includes insulated gauntlet gloves, hard-toed high-top shoes, leather aprons, insulated coveralls, safety glasses, helmets and hard hats, and leggings or high boots. Workers should always keep their clothes fully buttoned and uncuffed when performing hot work and wear wool or insulated fabrics. When welding overhead objects, workers will need extra protection, like heat-resistant shoulder covers, aprons, head covers, leggings, and suits. You must provide most types of PPE to your employees and train them on how to properly use, maintain, and dispose of it.
Hot work is dangerous and even deadly, but with proper training and protective measures, your facility can reduce welding-related injuries and illnesses. Follow all precautions for hot work and remove or cover flammable and combustible materials before your employees begin. Ensure that all employees are provided with PPE and use it correctly.