Verifying Safeguards Meeting Kit
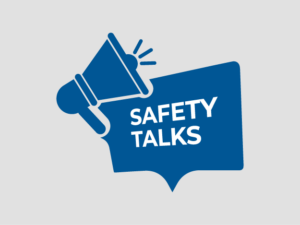
Verifying Safeguards Safety Talk
There are many safeguards that we put into place every single day to ensure that hazards are eliminated or mitigated. Often times another individual may be the one responsible for implementing safeguards for a work task. No matter if you or someone else is responsible for implementing a safeguard, safeguards should be verified that they are in place prior to beginning work.
HAZARDS FOR WORKERS
A safeguard is solution or a combination of solutions that eliminates or reduces the risk of exposure to hazardous moving parts or other harmful conditions. Things that put workers at risk of injury when working around machinery include:
- Rotating parts on shafts, couplings, feed rolls, and V-belts.
- Reciprocating or sliding parts as dies in punch presses.
- Parts that fragment or rupture such as abrasive wheels.
- Toxic or corrosive chemicals.
- Heat, noise, and vibration.
- Non-ionizing radiation such as ultraviolet (UV) light.
RISK
“Risk” means “a chance of injury or occupational disease.” The three most important factors that affect risk are severity, exposure, and probability:
Severity — If an incident occurred, how serious would the injury be?
Exposure — What is the extent of the workers’ exposure to the hazard?
Probability — How likely is it that an incident will occur?
WHY VERIFY
When individuals proceed with their work without verifying the proper steps have been taken to work safely, incidents can occur.
Examples
- Pausing before the startup of a machine to verify that everyone is out of the line of fire.
- Attempting to start up a piece of equipment after locking and tagging it out prior to beginning mechanical work.
- Doing a radio check with the other workers involved in a critical lift prior to beginning lifting operations.
- Making radio communication with an operator of heavy equipment to ensure that he waved you on to enter their work area.
- Going through a checklist of all necessary safeguards prior to beginning a complex work task.
WORKER TRAINING
Specific and detailed training is therefore a crucial part of any effort to provide safeguarding against machine-related hazards. Thorough operator training should involve instruction or hands-on training in the following:
- a description and identification of the hazards associated with particular machines.
- the safeguards themselves, how they provide protection, and the hazards for which they are intended;
- how to use the safeguards and why.
- how and under what circumstances safeguards can be removed, and by whom (in most cases, repair or maintenance personnel only).
- when a lockout/tagout program is required.
- what to do (e.g., contact the supervisor) if a safeguard is damaged, missing, or unable to provide adequate protection.
This kind of safety training is necessary for new operators and maintenance or setup personnel, when any new or altered safeguards are put in service, or when workers are assigned to a new machine or operation.
MINIMUM GENERAL REQUIREMENTS OF SAFEGUARDS FOR WORKERS SAFETY
Prevent contact: The safeguard must prevent hands, arms, and any other part of a worker’s body from making contact with dangerous moving parts. A good safeguarding system eliminates the possibility of the operator or another worker placing parts of their bodies near hazardous moving parts.
Secure: Workers should not be able to easily remove or tamper with the safeguard, because a safeguard that can easily be made ineffective is no safeguard at all. They must firmly be secured to the machine.
Protect from falling objects: The safeguard should ensure that no objects can fall into moving parts. A small tool which is dropped into a cycling machine could easily become a projectile that could strike and injure someone.
Create no new hazards: A safeguard defeats its own purpose if it creates a hazard of its own such as a shear point, a jagged edge, or an unfinished surface which can cause a laceration.
Create no interference: Any safeguard which impedes a worker from performing the job quickly and comfortably might soon be overridden or disregarded. Proper safeguarding can actually enhance efficiency as it can relieve the worker’s apprehensions about injury.
Allow safe lubrication: Locating oil reservoirs outside the guard, with a line leading to the lubrication point, will reduce the need for the operator or maintenance worker to enter the hazardous area.
FINAL WORD
We are human, we make mistakes. It is important to take the time to not only implement the safeguards that need to be in place, but also verify that they are indeed in place and functioning correctly. It never hurts to double check your own work or the work of those around you when dealing with the mitigation of hazards.