Shortcuts are a Choice Meeting Kit
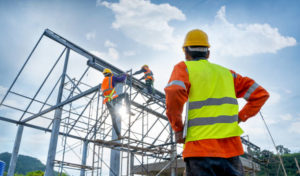
The decision to take a shortcut can be influenced by many different factors. That being said, at the end of the day shortcuts are a choice made by an individual.
DANGERS OF SHORT – CUTS
Shortcuts are generally derived from indolence in an attempt to perform a job with the most minimal effort required. This creates the opportunity for negative results and possibly severe consequences.
COMMON SAFETY SHORTCUTS
When it comes to safety taking shortcuts can manifest in many different ways. Examples:
- Almost every work task has several safeguards that are to be implemented prior to work beginning. Each safeguard that is implemented is one more way to protect yourself and others from injury.
- PPE is the last line of defense for workers. You never know when you may need it.
- Rushing during tasks or not taking the necessary time to do certain tasks. Many things can be missed when rushing during a work task. This can lead to incidents occurring.
ELIMINATE THESE 10 WORKPLACE SAFETY SHORTCUTS
1. Lifting Quickly: When lifting something really heavy, you should use a back brace, lift with your legs and even get other people to help share the load.
2. Skipping Breaks: By letting your mind and body recover for even just a few minutes at a time, you will be able to work more safely. Taking a lunch is even more important, as it will help you to regulate blood sugar so you can work more safely for the rest of the day.
3. Using Tools Improperly: Each tool has a specific purpose and job, which it will perform properly.
For example, trying to pound a nail into wood with the back end of a screw driver, rather than going to get a hammer. This can not only break the screwdriver, but it exposes the user to a lot of unnecessary danger.
4. Applying the Wrong Safety Label Stock: Using safety labels is one of the best ways to convey information throughout the facility. When making labels, however, you need to make sure you are using the proper type of label stock at all times, based on where the label will be placed. Look at the following examples colon.
- High Temperature Locations
- Cold Temperature Locations
- Oily or Greasy Locations
- Wet or High Humidity Locations
5. Ignoring ‘Near Misses’: When there is a major accident or injury in the facilitiy, everyone knows that they need to report it, fill out the proper paperwork and usually have an investigation into the cause. This is, of course, a good thing. For every actual accident or injury, however, there are often several ‘near misses’ where something went wrong, but nobody was hurt.
Remember, today’s ‘near miss’ is tomorrow’s accident if it is not prevented.
6. Insufficient Emergency Equipment: Most facilities will need to meet a set minimum for things like the number of fire extinguishers or emergency eye wash stations in the facility.
Someone responsible for the safety of the facility should identify areas where there are specific risks, and make sure the proper emergency equipment is located nearby.
7. Neglecting Cleaning Tasks: There are often many areas of the facility that need to be properly cleaned beyond just sweeping up messes or cleaning up spills.
One area is safety signs. They need to be wiped down. Dust, dirt, grease and other things can build up on them, making them very difficult to read.
8. No Clear Emergency Exit Path: Facilities typically have to have all the exits clearly marked with an easy to read sign that lights up in the dark. Due to large machines and the extensive floor space in most facilities, it can be difficult to see where exits are located, especially during an emergency.
To help ensure everyone knows exactly where they should go no matter where they are in the facility, it can be a good idea to add some sort of floor markings that always point people toward the nearest exit.
9. Only Initial Training: It is essential to provide high quality safety training to all employees when they are hired on, and then continue to give updates to this training on a regular basis.
10. Inadequate Maintenance: Keeping the machinery in your facility up to date and well maintained is absolutely essential to the safety of the entire company.
Make sure you have the general maintenance requirements of each machine well documented so that nothing is missed.
Avoid Safety Shortcuts: It is always much better to do something properly the first time than to have to either redo it again later or deal with the consequences of the shortcut down the road.
WAYS TO AVOID TAKING SHORTCUTS BY WORKERS
- Hold yourself to a higher standard. Do not take the easy way out. Take the time and energy to perform tasks correctly. Make it a habit to follow safety policies and procedures.
- Help set the expectation that shortcuts are unacceptable when it comes to safety.
- Realize that shortcuts affect more than just you. They can result in negative impacts on production, property damage, as well as injuries.
- If facing a perceived time pressure, evaluate whether it is a self-imposed time pressure. Individuals put pressure on themselves to perform a task faster when there is no outside pressure to get a work task completed.
- Preplan work tasks ahead of time so the necessary tools, training, personnel, safety equipment are available.
FINAL WORD
To boil it down taking shortcuts is just an individual choice. Sure there are many factors that affect whether an individual will make the choice to do so, but it is ultimately a choice that is made. It can be difficult to never take a shortcut when it comes to safety, but there are many actions that can utilized to eliminate the urge to do so.