Safety Attitude How to Get Workers to Develop One
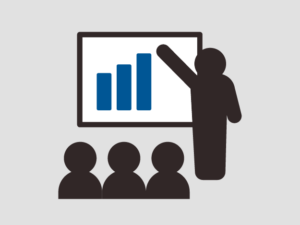
Getting workers throughout your company to display a “safety attitude” is the key to a safe and healthy work environment. Of course, that’s easy to say. The hard part is to actually cultivate such a safety attitude among your workforce. Here’s what safety trainers can do to achieve this objective.
The Challenge of Gaining Buy In
The biggest challenge is establishing and maintaining a safety conscious work environment. That’s a tall order and a full-time job. Sure, you might think and eat safety every day; but that’s not enough to get other people in the company to do the same.
By definition, a safety culture has to be experienced company-wide. The commitment must exist at all levels, including workers, supervisors and managers. Of course, buy-in at the upper levels is of critical importance. After all, if the rest of the management team’s agenda conflicts with this goal — such as an agenda that stresses maximizing production and output without regard for employees’ safety and welfare — then there’s no way the culture will be created.
The Role of Upper Management
You must have full support and buy-in from the top of the organization where the marching orders are initiated. Your task is to harness upper management’s muscle behind your culture building efforts. That involves working with your safety director to secure management’s help to:
- Promote safety to the Big 3: Safety must be recognized and included with the same importance as the “big three” – Quality, Delivery and Productivity. Safety can’t be the odd man out. It can’t be taken into consideration only when problems arise, or else problems will arise.
- Make safety everyone’s job: Every job description in the organization should include safety-related responsibilities and every employee should be held accountable for fulfilling these responsibilities.
- Establish safety goals: Quarterly and annual goals are set for the “big 3.” The same should apply for safety metrics. Establish the goals, monitor them, display them and celebrate accomplishments along the way. Accordingly, the company’s success should be measured in part on the achievement of safety goals and the responsibility must be everyone’s in order to achieve the goals for that success.
- Make safety a corporate mission: That corporate mission statement that you see hanging in a company’s reception area and board room generally includes a nice statement about satisfying the customer by providing a quality product. That’s all well and good. But if there isn’t also a reference to the company’s commitment to maintain a safe and healthy work environment, then odds are you’re looking at a company that doesn’t have a true safety culture.
From Preaching to Practice
Once you have gained the corner office’s commitment to a safety culture, everything just takes care of itself and health and safety nirvana is achieved. Right? Wrong. Sorry, but this is just the beginning of the challenge. The really tough task lies ahead. That task is to get everyone in the company to follow the directive in that corporate mission statement. Now you must create a work environment where people actually do think and act safely on the job. And a big part of the burden to champion this effort and keep it going falls squarely on the shoulders of you and the company’s safety director. Let’s look at what you can do to build a company-wide safety attitude.
Start at the very beginning. As soon as a new employee walks in the door and before they can even set foot in the plant, give them a thorough safety orientation. This is the best and earliest opportunity to plant the seed of the “safety attitude.” A safety orientation establishes the importance of safety to the company by laying it out as a responsibility that goes along with being a good employee.
Share the Responsibilities
Good safety managers utilize their best resources, including:
- Managers & Supervisors. Managers and supervisors work with the employees on the front line every day and therefore can have the most consistent impact by:
-
- Setting an example;
- Carrying out the established safety guidelines and policies throughout the company; and
- Providing feedback for prevention and solutions to safety-related issues and problems.
- Workers. Once you have the buy-in and support from managers, the workers on the floor need to be involved. Create a plant-wide safety committee program with representatives from all areas and shifts in the facility, so that everyone has a voice in safety issues.
- Safety Committee. How many safety committees just meet, talk and complain? How many more propose ideas, solutions, changes and actions, but have no authority or commitment to follow through and implement any of their proposals? The ineffectiveness of a committee will quickly undermine your progress. And it’s much more difficult to win back the support and confidence lost along the way. A good safety committee must be consistent and active and it must produce visible results. Once you have an effective, working safety committee with good representation and support at all levels of management and on the shop floor, then you have a good foundation to support your safety program and a medium for continuous two-way communication.
Lead by Example
Your safety attitude must be contagious. You must be seen not as the enemy trying to impede the process, but as someone dedicated to a safer work environment, fighting for everyone’s safety every day.
Your workers need to see and feel the company’s commitment to providing a safe and healthy work environment. Seeing improvements or changes made in the name of safety demonstrates management’s dedication and goes a long way to getting everyone involved.
Discipline is also an important part of the program. View the individuals in your workplace as a safety team with your role being to constantly recruit players. Those who blatantly undermine the team by continuously ignoring safety and putting others at risk don’t belong on the team or in the company. Safety rules must be consistently and firmly enforced to let everyone know that following established safety policies is just as important as quality, delivery and productivity.
Never Give Up
Having the support and resources of everyone makes a world of difference when you can’t be everywhere, 24/7. You need to allocate time and energy to other important EHS-related responsibilities, such as training, operating permits, licenses, inspections, as well as OSHA, EPA and local regulatory requirements. Hey, someone has to drive the bus and that’s you.
You need to keep everyone thinking and acting safely every day. That requires effort. Make yourself accessible, encourage suggestions and show your commitment by implementing changes and improvements that make for a safer work environment.
Conclusion
The safety attitude is the all-important “intangible” that every team or program must have to be successful. You can’t touch it, but you can feel it. You can also feel it when it’s missing. The absence of a safety attitude is what we fight against every day to avoid the most hated word in the supervisor’s vocabulary: “accident.”