Safety and OSHA Inspection Checklists – Quick Tips
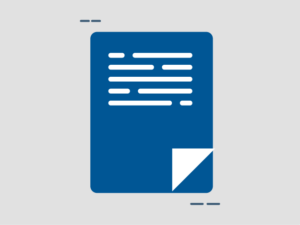
The most widely accepted means to identify workplace hazards is to conduct safety and health audits. One way to help understand a given situation is to look at it on a periodic basis. A survey conducted by the Occupational Safety and Health Administration (OSHA) in the late 1990s revealed that self-audits are performed for a number of reasons, with the three most common being:
- Careful inspections can reduce injury and illness rates within the workplace by identifying present hazards
- Staying on top of potential hazards is considered the right thing to do by many employers
- Performing self-audits and acting upon any findings helps sustain compliance with OSHA regulations.
Routine self-audits are a cost-effective method of not only identifying safety hazards that need to be corrected, but also for helping ensure compliance with OSHA regulations. Costs associated with occupational safety and health hazards, beyond potential fines, can be reduced if hazards are corrected. Man-hours lost through workers’ compensation and sick leave can be reduced and productivity can remain high. Some insurance carriers in partnership with OSHA offer reduced premiums to employers who perform self-audits.
The most thorough means for performing a self-audit is to use a checklist for each work area. The size and diversity of the business dictates how many checklists are required and how much detail should be in each. While there is no standard checklist format, several key features should be included:
- Name of auditor and date inspected
- Description and specific regulatory citation for all pertinent regulations with a space to note deficiencies
- A feasible completion date for deficiencies found
- Initials and/or date when all corrections have been completed
Workplace Checklist
The following is an example of what a portion of a workplace OSHA checklist could look like for a flammable storage area. Appropriate components depend on individual situations.
INSPECTION REPORT FOR FLAMMABLE STORAGE AREA
Location:
Inspected By:
Date of Inspection:
(Circle all numbers with deficiencies)
Containers
- Are approved containers and portable tanks used for the handling and storage of flammable liquids? 29 CFR 1910.106(d)(2)(i)
- Are portable tanks equipped with sufficient emergency venting to relieve internal pressure under fire conditions? 29 CFR 1910.106(d)(2)(ii)
- Are Table H-2 compliant sized flammable liquid containers in use? 29 CFR 1910.106(d)(2)(iii)
- Are not more than 60 gallons of Category 1, 2, or 3 flammable liquids, or more than 120 gallons of Category 4 flammable liquids stored in a storage cabinet? 29 CFR 1910.106(d)(3)(i)
- Do flammable liquid storage cabinets meet applicable design and construction requirements? 29 CFR 1910.106(d)(3)(ii)-(d)(3)(ii)(b)
- Is the use and handling of flammable liquids only incidental to the principal business? 29 CFR 1910.106(e)(2)(i)
- Are all flammable liquids stored in tanks or closed containers? 29 CFR 1910.106(e)(2)(ii)
- Do the quantities of flammable liquids stored outside an inside storage room or storage cabinet in a building or in any one fire area of a building exceed the maximums allowed (25 gallons of Category 1 in containers; 120 gallons of Category 2, 3, or 4 in containers; or 660 gallons of Category 2, 3 or 4 in portable tanks)? 29 CFR 1910.106(e)(2)(ii)(b)-(e)(2)(ii)(b)(3)
- Are adequate precautions taken to prevent the ignition of flammable vapors? 29 CFR 1910.106(e)(6)(i)
- Are containers of Category 1, 2 and 3 flammable liquids with a flash point of less than 100 °F (37.8 °C) grounded and bonded to containers during dispensing? 29 CFR 1910.106(e)(6)(ii)
Fire Extinguishers
- Are approved fire extinguishers mounted, located and identified so that they are readily accessible to employees? 29 CFR 1910.157(c)(1)-(c)(2)
- Are all fire extinguishers maintained in a fully charged and operable condition and kept in their designated places at all times except during use? 29 CFR 1910.157(c)(4)
- Are all fire extinguishers inspected and recharged regularly, and marked on inspection tags? 29 CFR 1910.157(e)
- Are the portable fire extinguishers provided for employee use, selected and distributed based on the classes of anticipated workplace fires? 29 CFR 1910.157(d)(1)-(d)(6)
- Are all portable fire extinguishers properly inspected, maintained and tested? 29 CFR 1910.157(e)-(f)(16)
- Upon initial employment and at least annually thereafter, have employees been provided training on the general principles of fire extinguisher use and the hazards involved with incipient stage firefighting? 29 CFR 1910.157(g)-(g)(4)
Exits
- Are exit routes and safeguards properly designed and maintained to minimize the danger to employees? 29 CFR 1910.37(a)-(a)(1)-(a)(4)
- Are exit routes adequately lighted and marked? 29 CFR 1910.37(b) – (b)(7)
- Are exit routes maintained during construction, repairs or alterations? 29 CFR 1910.37(d) – (d)(3)
Correction completion date:
Corrections have been completed (initials and date):
Supervisor:
Date:
Regulations and Record Keeping Standards
Below are two lists. The first highlights major General Industry regulations that are relevant to most work areas. The second details standards that require a written plan or program to be in place when applicable. These lists may not be all-inclusive and may not apply to all work areas.
Work Areas
All work areas should be identified and the applicability of each section of the OSHA standards from Title 29 of the Code of Federal Regulations (CFR) should be considered:
- Walking-working surfaces
see 1910.21 to 1910.30 - Exit routes and emergency planning
see 1910.33 to 1910.39 - Powered platforms, manlifts and vehicle-mounted work platforms
see 1910.66 to 1910.68 - Occupational health and environmental control – ventilation, noise and radiation
see 1910.94 to 1910.98 - Storing and handling of hazardous materials
see 1910.101 to 1910.126 - Personal protective equipment (PPE)
see 1910.132 to 1910.140 - General environmental controls – sanitation, marking physical hazards, permit-required confined spaces and lockout/tagout
see 1910.141 to 1910.147 - Medical services and first aid
see 1910.151 to 1910.152 - Fire protection
see 1910.155 to 1910.165 - Compressed gas and compressed air equipment
see 1910.166 to 1910.169 - Material handling and storage – use and care of forklifts, cranes, derricks, helicopters and slings
see 1910.176 to 1910.184 - Machinery and machine guarding
see 1910.211 to 1910.219 - Hand ad portable powered tools and other hand-held equipment
see 1910.241 to 1910.244 - Welding, cutting and brazing
see 1910.251 to 1910.255 - Special industries
see 1910.261 to 1910.272 - Electrical systems standard design, safety-related work practices and maintenance requirements
see 1910.301 to 1910.399 - Commercial diving operations
- see 1910.401 to 1910.430Toxic and hazardous substances
see 1910.1000 to 1910.1499
Record Keeping
In addition to a work area checklist, written programs, plans and procedures are often required by OSHA. The following standards require a written plan or program to be in place where applicable:
Creating and maintaining a checklist for General Industry operations is by no means the final step. When beginning a safety audit program, several ideas should be kept in mind. A team approach to safety is most effective; rotating people on and off the team will keep ideas fresh and enhance perspective. Inspect thoroughly and frequently; any area, regardless of size, can pose hazards that can crop up seemingly overnight. Once hazards are identified, have a system in place for correction.
Q: Are self-inspections necessary?
A: Yes. Self-inspections are an essential and recognized means to identify potential workplace hazards. The only way to be certain of an actual situation is to look at it directly from time to time. Organizations must know where potential hazards exist and whether they are under control.
Sources
(Rev 11/18)
The information contained in this article is intended for general information purposes only and is based on information available as of the initial date of publication. No representation is made that the information or references are complete or remain current. This article is not a substitute for review of current applicable government regulations, industry standards, or other standards specific to your business and/or activities and should not be construed as legal advice or opinion. Readers with specific questions should refer to the applicable standards or consult with an attorney.
Source: Grainger Know How – https://www.grainger.com/know-how