Roller Safety
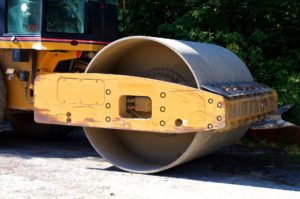
WHAT’S AT STAKE?
Workers who operate or work around roller/compactors are at risk of injury from a machine rollover or being struck by the machine or its components. Injuries and deaths can be prevented through wider use of rollover protective structures (ROPS) and seat belts on roller/compactors, training, establishing and adhering to safe work practices and procedures, and using appropriate personal protective equipment.
No cost is greater than the loss of human life, especially considering these accidents are preventable. The following reminders about compaction roller safety are just as applicable to any other construction equipment.
Newer compaction rollers are designed to be more stable. They have a lower center of gravity, wider base and low speed options. But when your jobsite terrain is hilly or you’re working an embankment, every machine is at risk of rolling over.
WHAT’S THE DANGER?
The two common causes of injury are machine rollovers and being stuck by the moving machine.
Compaction rollers should have two critical safety features
ROPS. Do not operate a machine that isn’t equipped with a rollover protection structure. This is the only thing that will keep the operator from getting crushed if the equipment does roll over.
Reliable seat belts. Always wear your seat belt – it’s the only thing that will keep the operator in place within the ROPS in the event of a rollover. Do not operate a machine with damaged or worn seat belts – replace them first. Make sure seat belts are adequately sized, too, because if they don’t fit properly they won’t work.
HOW TO PROTECT YOURSELF
Safety while in motion
Always wear your hard hat, when inside an enclosed cab. Even when you’re wearing your seat belt, it’s easy to hit your head on some hard surface in an accident.
If you’re working near a slope, operate the machine so your seat is parallel to the edge. With the end constantly in sight, you can stay far enough away to prevent the roller or wheels from slipping onto the slope.
If you get too close for some reason, immediately stop the machine and set the parking brake. Dismount so you can assess whether it will be safer to move forward or backward to get back onto the flat surface.
If you’re working on a slope, always drive the machine up or down, never along the side of the hill. Angled operation makes the machine more vulnerable to sliding or tipping.
When traveling on a grade, use a low speed and do not change gears.
Never park the machine on sloping ground unless you have no choice. If you must park near a slope, at least be sure the footing is firm so the equipment won’t slide.
Never exit the machine without first setting the parking brake.
What to do if machine tips over
There are several things you can do to reduce your risk of injury. Most important is to stay in place – trying to jump out of the cab is the riskiest thing Roller Safety you can do because it increases the chance you will get caught under the ROPS. Instead, prepare for the impact by:
- Pull your elbows and knees in close to your body.
- Holding on tightly.
- Leaning uphill (away from the impact).
Employers, manufacturers, and rental establishments should take the following protective steps for workers from injury while working with ride-on roller/compactors.
- Site Set-Up
- Develop site-specific safety plans for all aspects and stages of the job. Have plans analyzed by a qualified person to determine the safest possible methods to perform the work.
- Minimize the presence of workers on foot near machinery.
- Provide all workers on-site with training in sitespecific safety procedures and in hazards they may encounter at the site.
- Use barriers to separate workers, pedestrians, and vehicles from moving equipment.
- Use visual aids to identify edges.
- Continually evaluate safety plans to address changing conditions at the worksite.
- Provide appropriate personal protective equipment (PPE) such as high-visibility reflective vests and hard hats, and ensure that workers use and maintain them.
- Use machinery equipped with ROPS and seatbelts, and ensure their use. Replace seatbelts if they are damaged, worn, or too small.
- Contact equipment manufacturers or equipment dealers to determine whether approved retrofit ROPS and seatbelts are available for machinery without these safety features.
- Ensure that machines are not operated on grades steeper than those specified by the manufacturer.
- Establish a documented maintenance program for all machinery.
- Replace worn or damaged warning labels on machinery.
- Ensure that operators’ manuals are present on all machinery or available to the operator.
- Make sure that all the manufacturers’ safety features are operational.
- Ensure that all site workers comply with all applicable requirements of machine warning labels and operator manuals.
- Equipment Operator
- Take training in safety procedures at the site and in the proper use of the equipment. Follow manufacturers’ specifications and recommendations.
- Check work areas for workers on foot in the machine’s path before moving the machine or changing the direction of travel.
- Use spotters or barriers where necessary. Be aware of equipment blind spots.
- Be aware of the hazards associated with operating machinery on non-level surfaces. A competent person should continuously evaluate grades on which machinery is being operated to prevent rollover.
- Do not operate machinery without the ROPS and seat belts supplied by the manufacturer. Do not remove the ROPS or seatbelts.
- When capable, ensure that when rolling edges, the seat is positioned parallel to the edge to ensure visibility when working in close proximity to leading edges.
- Wear the seat belt and do not jump from the equipment in the event of a rollover. Keep knees and elbows close to the body, hold on firmly, and lean away from the impact to avoid being crushed by the ROPS.
- Conduct daily or pre-shift visual and operational checks on all equipment systems and operating controls before working the machine.
- Make sure that all the manufacturers’ safety features are operational.
- Comply with all warning labels.
- Other Site Workers
- Take training to recognize and avoid unsafe conditions and follow required safe work practices that apply to the work environment.
- Be aware of the hazards and blind spots associated with working near moving equipment.
- Before each work shift begins, review and con- firm communications signals to be used between equipment operators and workers on foot.
- Do not approach machinery without first signaling the operator to shut down the equipment and receiving acknowledgment from the operator.
- Do not ride as a passenger on rollers or similar mobile equipment.
- Do not rest or lean against any equipment.
- Wear PPE that is provided, such as high visibility reflective vests and hard hats, to increase visibility. Equipment Manufacturers
- Ensure that ROPS and seatbelts installed on a ride-on roller/compactor meet specific Society of Automotive Engineers (SAE) minimum levels of performance [SAE 1994, SAE 1997].
- Consider equipping machinery such as rollers that must change direction frequently with sensors to detect the presence of persons in the machine’s path. This would provide site workers with an additional safety control.
- Clearly identify and label all machine controls.
- Consider providing multilingual warning labels and operator manuals.
- Equipment Rental Establishments
- Include only ROPS- and seatbelt-equipped machines in fleet selection.
- Establish a documented preventive maintenance program for machinery.
- Provide training for customers upon delivery.
- Provide customers with machine-specific safety brochures.
- Ensure that operators’ manuals are located on machines or are available to operators.
FINAL WORD
Operators simply must be more vigilant and more careful in order to protect themselves. Here’s how you – and they – can remain productive while focusing on jobsite safety.