Power Press Safety Meeting Kit
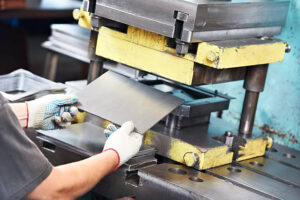
A press is a machine that uses pressure to change the shape of a workpiece by rolling, forming, forging, punching, stamping, bending, piercing, drawing, etc. Presses are classified by the work they perform as well as their power source: manual driven, mechanical, hydraulic, or pneumatic.
TYPES OF POWER PRESSES
full revolution (positive clutch) ? once activated, it cannot be stopped until the press cycle is completed by lowering and raising of the slide or ram. Presence sensing devices will not work on these machines. Operators must be protected by fixed guards or mechanical interlock guards during the entire operating cycle.
part revolution or friction clutch ? can be disengaged at any time before it completes the down stroke. Can be guarded with presence-sensing devices.
THE MAIN CAUSES OF POWER PRESS ACCIDENTS ARE LACK OF TRAINING, LACK OF EFFECTIVE GUARDING, AND BYPASSING OF GUARDS.
- Untrained operators using complicated and potentially dangerous machinery are a threat to themselves and their coworkers. No employee is to operate a power press without training on safe operating techniques.
- Guards between the operator and the point of operation must be designed to prevent the operator from reaching under the ram during the downward stroke. If guards are not used or not working properly, an accident is likely to occur.
- Unsafe working conditions can be created if an employee attempts to bypass press guards and interlocks or reaches in to clear a part while the press is running.
GREATEST DANGER FOR WORKERS
Employees work with power presses face the greatest danger of injury at the point of operation where the stock is inserted, held and withdrawn by hand. That is why effective machine guarding is crucial for keeping hands, arms or other parts of the body from making contact with dangerous moving parts.
GUARDING PREVENTION
Safeguards should be designed so they can?t be easily tampered and removed, don?t create a new hazard, or don?t impede a worker from performing the job. Point-of-operation guards and devices can include light curtains, barrier guards, two-hand controls, and restraints.
Guards should be designed to prevent workpieces or offcuts from being ejected while under pressure and expose operators to a hazard.
Adequate guards must be provided. Some power press injuries are caused by relying on the operator to synchronize the movement of their hand with the operation of the foot pedal.
WHAT WORKERS NEED TO DO TO AVOID POWER PRESS INJURIES
Check the power press at the beginning of each shift, following each new die setup, and when operators change. Make sure all parts, auxiliary equipment, and safeguards are in place, properly adjusted, and in safe operating condition.
At least once per week, conduct a functional performance check to ensure components are operating safely and complete all necessary maintenance or repairs before the press is returned to operations.
TRAINING IS THE MOST IMPORTANT ELEMENT IN ELIMINATING ACCIDENTS
- How to use all press controls.
- Where each safety device is located on the machine and how to use it correctly.
- How to use tools to remove ?stuck work? and how to use swabs, brushes or oil cans to lubricate dies.
- Why, when and how to use personal protective equipment, such as safety glasses, gloves, safety shoes and hearing protection.
- Where to store parts, tools, die sets, bolster plates to prevent falling hazards.
- Where possible pinch points with moving components are located.
- The importance of keeping the work area clean and orderly.
- Not to operate the press until it has been checked and tested prior to production operations.
- How to report problems.
BEST WORKPLACE SAFETY MEASURES WITH POWER PRESSES
- All personnel involved in any aspect of working with a mechanical press need to be made aware of the safety dangers that exist and the proper methods to be used with the machine.
- Safety signs should be posted in the proper areas in all the languages spoken by the workforce. Never post a safety sign on the mechanical press guard.
- All controls and electrical components should be updated following any new legislation.
- It is essential that the light curtains are positioned correctly on the power press.
- Workers must be required to follow all safety procedures of the mechanical press including locking out and returning controls of the mechanical press to their proper settings and configuration.
- Equip presses with properly designed and constructed point-of-operation guards.
- Establish a press maintenance and inspection program and ensuring regular and periodic inspections.
- Develop, implement, train and ensure workers to use safe work practices, power press controls, and safety guards and devices, including lockout/tagout training.
FINAL WORD
Anyone operating or near a mechanical press needs to be aware of the dangers and use their best judgment along with their common sense in all aspects of their work.