Plastic Molding Safety Meeting Kit
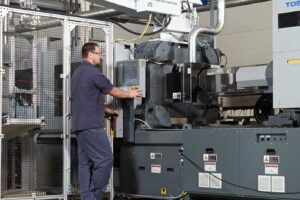
WHAT?S AT STAKE
The plastic molding industry uses powered machines such as rollers, presses, compression plates, heat sealers, and cutting knives to form plastic products. The moving, rotating, cutting, and hot equipment you use in plastic molding poses safety hazards.
WHAT?S THE DANGER
INJECTION MOLDING HAZARDS
Plastic injection molding involves mechanical and thermal hazard sources, where users can experience burns, crushes, impacts, and other dangers. Improper safety procedures jeopardize the longevity of machines and lead to operator injury.
Mechanical/Thermal Hazards of Injection Molding
- Mold Area
- Clamping mechanism area
- Core and ejector drive
- Nozzle area
- Injection unit area
- Feed hopper/opening area.
- Heater bands/heat source areas
- Parts discharge area
- Hoses in/around the machine
- Inside the guard and outside mold areas
- Part inserts and removal areas.
Electrical Hazards
- Electromagnetic component disturbances
- Stored/residual energy areas.
Other Hazards
- Vapors and gasses
HOW TO PROTECT YOURSELF
SAFETY RULES FOR INJECTION PLASTIC MOLDING OPERATIONS
- Before even touching the machine, all operators must be adequately trained in machine operation, workspace management, and proper lockout/tag-out protocol.
- Operators should never reach over or under machine guards, stick appendages into the hopper/granulator, or stand directly below a suspended mold.
- PPE such as safety glasses, safety shoes, and respirators (if required) should always be worn during operation.
- Should never free climb on the machine, horseplay around the area, or leave catwalks/railed platforms when needing to climb the machine.
- Training must be provided on the chemical hazards associated with the injection molding process, both with regard to the material and any supporting chemicals such as mold release, lubricant, etc., used in the injection molding process.
- Every worker should know the location and route to fire extinguishers, fire exits, and emergency tools.
- Operators should double-check that the nozzle tip is firmly in place and correctly centered prior to molding.
- The machine and its platform are free of debris, past materials, oil, water, etc., and no vital safety equipment/devices are missing.
- All safety equipment (especially eye protection) is present, undamaged, and operative.
- Fire extinguishers, first aid kits, and personal protective equipment are present and readily available in needed quantities as per work staff numbers.
- The environment around the machine is clean and free of slipping hazards such as oil or water leaks on the ground.
- All tooling and equipment are in good condition.
- All temperatures in the barrel, the hydraulics, and the mold are to the project’s specifications and are held during a cycle.
- All pressures in the barrel and the mold are to the project’s specifications and are held during a cycle.
- There are no plastic materials left inside, on, or around the machine before beginning operation, and no sprues, runners, gates, etc. within the barrel, nozzle, or mold cavity.
- All hoses and cords are fully intact with no damage to their insulation or cladding.
- All mold setup steps are followed as posted on the setup sheet/procedure before injection molding.
- Material should never be left in the mold. Remove the molded parts and sprue before shutting down the machine.
- Before working on the machine or between plates, be sure proper lockout procedures have been followed.
- When purging material from the plasticizing cylinder or changing materials, be sure of the compatibility of materials being used. Check with your supervisor for this information.
HOUSEKEEPING SAFETY REMINDERS IN PLASTIC MOLDING OPERATIONS
- Be certain all safety devices are working properly before operating the machine.
- If any safety equipment is missing, damaged, or inoperative, notify your supervisor immediately and do not operate the machine.
- Report any hazard to your supervisor, no matter how minor it is.
- Report any open receptacles, junction boxes, bare wires, oil leaks, or water leaks to your supervisor.
- Keep the platform and work area clean.
- Use safety devices provided and do not bypass, change, or otherwise make inoperative any such safety device.
- Never block fire extinguishers, fire exits, or other emergency equipment.
- Use only tools and equipment that are in good condition.
- When lifting, keep your back straight and lift with your legs. If the load is too heavy, get help or notify your supervisor.
- Report all injuries to your supervisor immediately.
- Be sure barrel and mold temperatures are maintained. Report deviations to your supervisor.
- Whenever you leave your machine, be sure it is turned off.
FINAL WORD
There are dangers involved in the injection molding process, specifically in using and operating injection molding machines. Proper maintenance and vigilance by operators will mitigate resultant problems.