Loading Dock Safety Meeting Kit
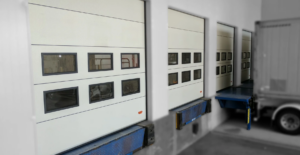
Loading and receiving docks are designed to facilitate smooth and efficient handling of shipping materials. Most docks have three basic machines to ensure this process is as productive as possible—trucks, forklifts, and cargo lines.
WHAT WORKERS NEED TO KNOW ABOUT LOADING DOCKS
After a semi-truck arrives, the driver drops off the trailer and heads on to their next assignment. Once disconnected from the truck, trailer creep may occur. This is where the trailer “creeps” away from the dock if its wheels are blocked or otherwise restrained, resulting in a gap between the dock and the trailer. Trailer creep also occurs each time a forklift operator enters or exits the trailer. Due to the weight of the forklift, the trailer can move even farther away from the dock, causing any initial gap to widen. As the gap grows, the risk for injury increases.
Before anyone enters the trailer, employees—not the truck driver—must secure the trailer with a wheel restraint device. The restraint system is designed to limit forward movement of a trailer but doesn’t always eliminate it. Employees need to monitor the trailer for movement throughout the loading and unloading process and reposition the trailer when a gap forms.
Three most common restraint systems are: Wheel chocks, Wheel-based restraints, Automated restraint.
LOADING DOCK HAZARDS
- Slips, trips and falls caused by floor conditions, poor housekeeping, or dock edge.
- Forklifts overturning.
- Pedestrian and powered truck collision.
- Trailer creep, which can cause a gap between the trailer and dock.
- Moving unsecured loads.
- Struck by and being crushed by an object or load.
- Back injuries from improper lifting or carrying.
- Inadequate lighting especially in the trailer.
- Carbon monoxide exposure from truck and powered material-handling equipment.
LOADING DOCK HAZARD CONTROL
- Shut off the engine and engaging the break while loading or unloading vehicle.
- Prevent trailer creep by using wheel chocks and vehicle restraints.
- Paint the edges of the loading dock to improve visibility.
- Provide physical barriers at dock edges when not in use.
- Ensure dock plates have appropriate capacity, stability, and proper placement.
- Prevent employees from riding on material handling equipment.
- Poste and enforcing speed limits for industrial trucks.
- Make sure all personnel are trained in dock safety.
- Provide adequate lighting at the dock and in trailers.
- Shrink-wrapping loose product for transport or storage.
- Maintain good housekeeping and cleaning up the area regularly.
INJURY PREVENTION AT THE DOCKS
- Secure the vehicles. Before loading and unloading, make sure to use vehicle restraints to secure trucks to the dock and forklifts away from the open bay doors.
- Maintain a safe distance as the truck backs into the loading area. While the truck is maneuvering into position, make sure the area around the trailer is clear, everyone in the docking area is at least ten feet from the door.
- Highlight the danger zones. Use brightly colored paint to designate the dangerous areas around the dock.
- Maintain a clean work environment. Try to keep all work surfaces clean and clear of any debris.
- Encourage patience and safety. Make sure everyone around you knows not to push boxes too hard or too forcefully as it can hurt those around them.
- Maintain all equipment. Make sure all equipment is in working order before you start the loading or unloading process. Routine inspections identify potential mechanical problems before they become accidents.
ENVIRONMENTAL SOLUTIONS
Loading docks and warehouses require a lot of light and sometimes a few burned-out lights or a cloudy day can cause people to miss seeing something potentially hazardous.
Dock seals should be regularly maintained or updated to ensure that they are tight, and that water or snow won’t seep in from the top of the docked trailer.
Adequate air conditioning should also be on the list, especially because of potential heat stress in the summertime when workers have to load or unload trucks.
ENGINEERING SOLUTIONS
A simple chain or a line suspended in the air may sometimes work as a visual reminder, but it certainly won’t prevent a forklift or a person from falling over the edge. Solid, strong barriers are readily available and easy to operate.
Sometimes trailers can separate or move unexpectedly, which means that securing them is vital to preventing people from falling through or being injured by sudden movements of forklifts, machinery, or materials. There are many devices that can help, such as vehicle restraints or wheel chocks.
Some companies might want to consider installing “walking floors” in their trailers or around loading docks. These floors can move various weights and often alleviate or completely remove the need for forklifts to drive inside the trucks, making loading and unloading safer.
Fire extinguishers are a must, and additional heat dissipation systems and multi-layer foil can prevent burning from trailer marker lights.
FINAL WORD
Safety is always a priority on frenetic loading docks but can only be maintained by training workers, safety signage, proper equipment usage, replace aging dock equipment and sound housekeeping.