Isocyanate Exposure, Reaction and Protection – Quick Tips
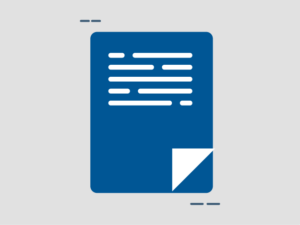
Introduction
Isocyanates are widely used and found in many industries and occupations, including painting, construction, shipbuilding, upholstery manufacturing and firefighting. Isocyanates have been used in the United States since the late 1940s. They are produced by reacting a primary aliphatic or aromatic amine dissolved in a solvent such as xylene or monochlorobenzene with phosgene dissolved in the same solution. This exothermic reaction forms polyurethane. This polyurethane is then used in the production of rigid or flexible foams, surface coatings, paints, electrical wire insulation, adhesives, rubbers and fibers.
The most common forms of isocyanates are toluene diisocyanate (TDI), methylene diphenyl diisocyanate (MDI) and hexamethylene diisocyanate (HDI).
TDI is a liquid at room temperature, and can cause asthma-like conditions when inhaled as an aerosol. TDI is a key ingredient in many spray paints and coatings. It’s used in flexible foams that are used in making cushions for automobiles, furniture and mattresses.
MDI is used in the manufacturing of rigid foams, and when heated causes asthma-like conditions when inhaled as an aerosol. This makes MDI somewhat less hazardous than TDI, so it has been replacing TDI in certain applications. MDI is commonly used in the production of adhesives, automobile bumpers, shoe soles, coated fabrics and spandex fibers. It can also be found in paints.
HDI is mainly used to make polyurethane foams and coatings it is also used as a hardener in automobile and airplane paint. Exposure can cause an allergic asthma-like response with coughing, wheezing and shortness of breath.
Some less common forms of isocyanates include:
- napthylene diisocyanate (NDI)
- polymethylene bisphenylisocyanate (PAPI)
Isocyanate Exposure Levels
The Occupational Safety and Health Administration’s (OSHA) permissible-exposure limit (PEL) for TDI and MDI is 0.02 part per million (ppm) in air as a ceiling limit (C). The ceiling is the highest concentration to which an employee can be exposed. The American Conference of Governmental Industrial Hygienists (ACGIH) recognizes 0.005 ppm as its threshold-limit value (TLV) as an eight-hour time-weighted average and 0.02 ppm as a short-term exposure limit (STEL) for TDI, MDI and HDI. A summary of exposure limits established for isocyanates can be found in Appendix B of the Isocyanate Compliance Directive (CPL 03-00-017)
Air Monitoring for Isocyanates
OSHA test method 42 (for TDI and HDI) and test method 47 (for MDI) spell out personal-monitoring procedures for isocyanates. Appendix B of the Isocyanate Compliance Directive (CPL 03-00-017) details the sampling protocols and sample shipment procedures.
You can also conduct continuous monitoring for isocyanates. Many companies offer single-point monitors that continuously monitor isocyanates for up to one month. They operate by an electro-optical sensing system, which uses a cassette-like tape. A stain occurs on the tape, and is then read in proportion to the concentration of the isocyanate. Different cassette tapes are available. Standard-play tapes are replaced every two weeks. Extended play tapes last for a month. Datalogging monitors with alarms are also available. These types of monitors are ideal in spray-booth operations.
Effects of Isocyanate Overexposure
Exposure to isocyanates can lead to chemical bronchitis and pneumonitis. An isocyanate reaction often includes coughing, tightness of the chest, shortness of breath, nausea, vomiting, eye and skin irritations, gastric pain and loss of consciousness.
Continuous overexposure to isocyanates can lead to pulmonary sensitization or “isocyanate asthma.” When this occurs, symptoms improve when the irritant is removed. However, acute asthma attacks occur on renewed exposure, even when the encounter is very brief or at low levels of isocyanates, and can cause death.
Skin contact can cause inflammation and necrosis, which might lead to dermatitis. Wash hands with soap and water immediately upon contact. It is important to use soap and vigorous washing of the hands because isocyanates are not readily water soluble making them difficult to remove from the skin or clothing.
National Emphasis Program
Due to the systemic health effects that isocyanates have on the body coupled with the wide range of industries and occupations where isocyanate exposure exists, OSHA took action in June of 2013 issuing the 3-year National Emphasis Program (NEP) targeting isocyanate exposure. OSHA has recently extended the NEP through June of 2019. The core purpose of the NEP for Isocyanates is to identify and reduce, or eliminate, the incidence of adverse health effects associated with occupational exposure to isocyanates through enforcement and outreach efforts. The goal is to raise awareness among employers, workers, and safety and health professionals of the serious health effects associated with occupational exposure to isocyanates.
Corrective Actions to Reduce Exposure
OSHA recognizes the “Three Lines of Defense” (see figure 1) as a way of thinking about and applying specific actions to reduce or eliminate potential exposures to identified hazards. This is a commonly used and understood practice within the safety community. In this philosophy you always apply the most effective method first, working down from there. This strategy begins with eliminating/engineering the hazards out and then implementing administrative controls such as policies and procedures. Lastly, if the first two lines of defense are not feasible or insufficient to adequately reduce exposure levels, then personal protective equipment (PPE) is to be used as the last line of defense. Preventing exposure to isocyanates is a critical step in eliminating the health hazard.
Lines of Defense
Figure 1: OSHA’s Three Lines of Defense
Solutions are presented in the NEP-Isocyanates to reduce isocyanate exposure based on OSHA’s Three Lines of Defense:
- Engineering controls such as substituting different chemicals or closed systems and ventilation to eliminate or minimize isocyanate exposure in the workplace.
- Administrative controls such as worker education, scheduled maintenance, work practice controls such as housekeeping, personal hygiene practices and isolation.
- PPE such as respirators, gloves and clothing to prevent inhalation or contact with isocyanates.
PPE for Handling Isocyanates
As part of the NEP for isocyanates, OSHA assesses the work environment for appropriate use of PPE under the following four categories: body protection, eye protection, respiratory protection, and hand protection.
Eye protection: Individuals working with isocyanate based products need to consider the use of appropriate eye and face protection. Isocyanate compounds can irritate the eyes and skin and are not water soluble so they can be difficult to remove, so exposure prevention is very important. The proper selection of eye protection is vital to prevent contact with the eyes and face. Where handling liquid isocyanate compounds and splash potential is present safety eyewear alone is not adequate. Non-vented or indirectly vented goggles worn with a face shield or a standalone full-face respirator provides liquid exposure protection.
Respiratory protection: Must be used in accordance to the requirements set forth in OSHA’s Respiratory Protection Standard (29 Code of Federal Regulations (CFR) 1910.134). OSHA states that use of air purifying (cartridge) respirators (APRs) is acceptable only if a cartridge change schedule is utilized (OSHA Interpretation Letter 2000). Change schedules will ensure the cartridge is not used beyond its life expectancy. If air concentrations of the isocyanate compound are not quantified or known, like in emergency situations, APRs cannot be used. In these situations a supplied air respirator (SAR) or self-contained breathing apparatus (SCBA) must be used.
Clothing/Gloves: Because various glove/clothing materials resist differently, no one glove/clothing is suited for all isocyanate compounds. A glove or garment that is well suited for one application may not be right for another exposure related task. It is best to base glove/clothing material selection on the manufacturer’s chemical resistance testing guide as well as considering other factors such as dexterity, comfort, temperature, seam construction, and overall durability. Based on the chemical guides and consideration of all factors, a glove or clothing garment that is most resistant to the chemicals being used and best suited for the job task should be selected. It is important to note that section 8 of the Safety Data Sheet (SDS) will not be brand specific. The actual chemical compatibility of a given glove or clothing garment material can vary between manufacturers. Selections must be based on the particular manufacturer’s test data.
Commonly Asked Questions
Q: Can I wear an air-purifying, cartridge-style respirator for protection against isocyanates?
A: Yes. Air-purifying respirators can be used with contaminants that have poor warning properties, such as isocyanates. However, you must check with the manufacturer of your respirator for specifics. For example, 3M and MSA have a respirator change-out formula for some isocyanates. If you know the airborne concentration in ppm, you can calculate about how long a cartridge will last. Please refer to Quick Tips #196: Respirator Cartridge Change Schedule for information.
Q: In what types of products are isocyanates commonly found? What types of occupations involve exposure to isocyanates?
A: Isocyanates are commonly found in automotive paints, foam cushions, mattresses, car seats, foam insulation, foam packaging materials, under-carpet padding, polyurethane rubber and adhesives. Some professionals who might encounter isocyanates are auto/truck-body repair-shop painters, insulation manufacturers, plastic wire coating and pipe manufacturers, and tire and furniture manufacturers.
Q: Are isocyanates considered a fire hazard? What type of fire extinguisher should be use to put out a fire that contains isocyanates?
A: Isocyanates have an approximate flash point of 527°F, OSHA defines a flammable liquid as a flash point under 199.4°F so Isocyanates are not considered a flammable liquid and do not pose a serious fire hazard. Fires may be extinguished with carbon dioxide or dry-chemical extinguishers. However, when isocyanates burn, they do become harmful to anyone who is not equipped with a SAR.
Sources
3M Job Health Highlights-Respirator Selection for Diisocyanates, Vol 18, August, 2009
What are Diisocyantes?, American Chemistry Council. 2016
OSHA National Emphasis Program – Occupational Exposure to Isocyanates Instruction Directive number CPL 03-00-017 Occupational Safety and Health Administration. June 2016
OSHA Standard Interpretation letter, Occupational Safety and Health Administration. July 18, 2000. (OSHA Interpretation Letter 2000)
“Guidance for Selection of Protective Clothing for MDI Users” American Chemistry Council. March 2013
“Guidance for Selection of Protective Clothing for TDI Users” American Chemistry Council. March 2013
“Occupational Hygiene Air Monitoring for MDI & TDI Guidance” American Chemistry Council. August 2012
The information contained in this article is intended for general information purposes only and is based on information available as of the initial date of publication. No representation is made that the information or references are complete or remain current. This article is not a substitute for review of current applicable government regulations, industry standards, or other standards specific to your business and/or activities and should not be construed as legal advice or opinion. Readers with specific questions should refer to the applicable standards or consult with an attorney.
Source: Grainger Know How – https://www.grainger.com/know-how