Incident Investigations
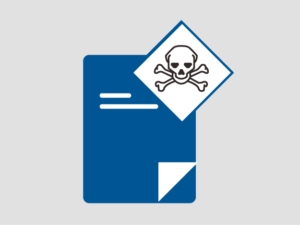
INCIDENT
It was an overcast, chilly, Saturday morning in May 2014 when a young worker in Kentucky lost his life in an industrial incident. An investigation into his death hopefully will save the lives of workers in the future.
On that morning – May 17, 2014, at 9 a.m. – a 21-year-old foreman and two coworkers were instructed to clean a Rapidmix 400 C industrial continuous mixing plant in preparation for a job the following week. The mixing plant, which had not been used or cleaned for several months, was located in the company’s lot next to the maintenance shop.
Once the foreman and two employees had cleared much of the dried, stuck-on concrete from the vein feeder, the foreman started the mixer section to remove the remaining debris, creating a cloud of dust. The foreman instructed the two employees to leave the area so they would not breathe in dust particles. He then stepped onto the mixer’s metal doors, intending to exit from the opposite side of the mixer.
Four doors covering the mixing section
The two pairs of doors that covered the opening of the mixer each measured 31½ by 53 inches. Each pair of doors was hinged in the center with two, 2-inch tall hinges. Each door opened and closed on the outer edge of the mixer unit, controlled by one interlock switch for the set of doors on the left and one interlock switch for the set of doors on the right.
Mixing Shafts
As the foreman shifted his weight onto one of the metal doors, the door collapsed into the mixer, along with the victim. By the time one of the employees hit the emergency stop switch, the young foreman was chest high in the 14-foot-long mixing shafts with 6-inch by 8-inch paddles; the shafts rotated at 110 RPM. A 911 call was placed, but the young foreman was pronounced dead at the scene.
Mixer Was in Need of Repair
The Kentucky Fatality Assessment and Control Evaluation (FACE) Program, federally funded to study occupational fatalities, investigated the case.
14 and 15, 2013, a service inspection was conducted on the mixing machine by a manufacturer’s service technician. During the inspection, the service technician made several recommendations for repair:
- The mixer safety switch needed to be replaced;
- One of the interlocks for the doors was missing and needed to be replaced since the doors could be opened while the auger was running;
- The outloading conveyor motor disconnect had broken off the frame and needed to be replaced; and
- The doors had broken hinges that needed to be repaired.
Broken door hinge on the metal door, covering the mixing section
On Nov. 27, 2013, the company ordered the suggested parts for repair. However, at the time of the incident, the interlock on the door still was missing, and the door hinges still were broken.
As a result of this tragic incident and the investigation, Kentucky FACE made the following recommendations for the prevention of future similar incidents:
- Employers should develop and implement written procedures for maintaining a Rapidmix 400 C continuous mixing plant to include pre-inspection, cleaning the mixing plant inside and out immediately after each use, making prompt repairs to broken parts such as door hinges and promptly replacing missing or damaged parts such as interlocks for the doors covering the mixing section.
- Employers should train employees on hazard recognition for all aspects of a job involving equipment such as the Rapidmix 400 C continuous mixing plant, including instructions not to walk or stand on the doors covering the auger section while operating the mixing plant.
- Employers should provide documented refresher training at least annually or prior to the mixing plant’s first use each year.
- Manufacturers should consider installing a switch so that the equipment doors cannot be opened during operation.
The loss of this young foreman’s life was a tragedy for both the employer and the young man’s family. Kentucky FACE uses the facts gathered from investigations to formulate and disseminate injury prevention strategies, with the hope of preventing future, similar incidents.
NEED TO KNOW
The following are facts that should be enough to make very employer stop and consider their
environments and workplace incident investigations techniques:
- According to the Bureau of Labor Statistics multiple workers die every day in American workplaces.
- 4 million serious injuries occur annually, not to mention all the sickness and disease cases resulting from stress and toxins.
Is there a difference between the term “accident” and “incident” in the context of the workplace? The term
“accident” has been used often in the past referring to an unplanned, unwanted event. Some people
suggest that “accident” was a random event that could not have been prevented!!! OSHA suggest that
nearly all worksite fatalities, injuries, illness are preventable.
The term “incident” is the appropriate term when referring to these events.
Incident reporting of all injuries including close calls is critical to the integrity of the workplace.
- It is impossible to create improved processes that protect workers if management is not aware of what kinds of problems are occurring in the workplace that may cause injury or property damage.
- The workplace is even at greater risk for a more serious incident to occur in the future if a minor incident or near miss is ignored or not reported.
- Failure for incident reporting will negate a process in which situations can be corrected to prevent similar incidents from occurring in the future.
- Employee participation in workplace safety improvement strategies will not be encouraged if incidents are not reported.
BUSINESS/ REGULATIONS
Investigation Procedure / Policy – Occupational Health and Safety Act, Section 8.1(1)
Every employer with 20 or more employees regularly employed in the Province shall establish a written health and safety program, in consultation with the committee or the health and safety representative, that includes provisions with respect to….
- (e) a system for the prompt investigation of hazardous occurrences to determine their causes and the actions needed to prevent recurrences;
- (f) a record management system that includes reports of employee training, accident statistics, work procedures and health and safety inspections, maintenance, follow-up and investigations;
STATISTICS
The Injuries, Illnesses, and Fatalities (IIF) program produces a wide range of information about workplace injuries and illnesses. These data are collected and reported annually through the Survey of Occupational Injuries and Illnesses (SOII) and the Census of Fatal Occupational Injuries (CFOI).
The latest numbers show.
Nonfatal Injuries and Illness, Private Industry for 2018.
Total recordable cases.
2,834,500
Cases involving days away from work:
900,400
Median days away from work:
8
Cases involving sprains, strains, tears:
308,630
Cases involving injuries to the back:
142,230
Cases involving falls, slips, trips:
240,160
Total fatal injuries (all sectors):
5,250
Roadway incidents (all sectors):
1,276
Falls, slips, trips (all sectors):
791
Homicides (all sectors):
453
A total of 5,250 workers died from a work-related injury in the U.S. in 2018, up 2 percent from the 2017 total of 5,147. The fatal injury rate was unchanged in 2018 at 3.5 per 100,000 full-time equivalent workers.
Employer-reported injury and illness rate unchanged in 2018 at 2.8 cases per 100 workers
The rate of nonfatal occupational injuries and illnesses among private industry employees was unchanged for the first time since 2012 at 2.8 cases per 100 full-time equivalent workers in 2018. Workers in private industry incurred 2.8 million injuries or illnesses in 2018.
RECOMMENDATIONS
At this stage of the investigation most of the facts about what happened and how it happened should be known. This data gathering has taken considerable effort to accomplish but it represents only the first half of the objective. Now comes the key question – why did it happen?
Keep an open mind to all possibilities and look for all pertinent facts. There may still be gaps in your understanding of the sequence of events that resulted in the incident. You may need to re-interview some witnesses or look for other data to fill these gaps in your knowledge.
When your analysis is complete, write down a step-by-step account of what happened (the team’s conclusions) working back from the moment of the incident, listing all possible causes at each step. This is not extra work: it is a draft for part of the final report. Each conclusion should be checked to see if:
- it is supported by evidence
- the evidence is direct (physical or documentary) or based on eyewitness accounts, or
- the evidence is based on assumption.
This list serves as a final check on discrepancies that should be explained.
The most important final step is to come up with a set of well-considered Recommendations designed to prevent recurrences of similar incidents. Recommendations should:
- be specific
- be constructive
- identify root causes
- identify contributing factors
Resist the temptation to make Only General Recommendations to save time and effort.
For example, you have determined that a blind corner contributed to an incident. Rather than just Recommending “eliminate blind corners” it would be better to suggest:
- install mirrors at the northwest corner of building X (specific to this incident)
- install mirrors at blind corners where required throughout the worksite (general)
Never make Recommendations about disciplining a person or persons who may have been at fault. This action would not only be counter to the real purpose of the investigation, but it would jeopardize the chances for a free flow of information in future investigations.
In the unlikely event that you have not been able to determine the causes of an incident with complete certainty, you probably still have uncovered weaknesses within the process, or management system. It is appropriate that Recommendations be made to correct these deficiencies.
The Written Report
The prepared draft of the sequence of events can now be used to describe what happened. Remember that readers of your report do not have the intimate knowledge of the incident that you have so include all relevant details, including photographs and diagrams. Identify clearly where evidence is based on certain facts, witness accounts, or on the team’s assumptions.
If doubt exists about any particular part of the event, say so. The reasons for your conclusions should be stated and followed by your recommendations. Do not include extra material that is not required for a full understanding of the incident and its causes such as photographs that are not relevant and parts of the investigation that led you nowhere. The measure of a good report is quality, not quantity.
Always communicate your findings and recommendations with workers, supervisors and management. Present your information ‘in context’ so everyone understands how the incident occurred and the actions needed to put in place to prevent it from happening again.
Some organizations may use pre-determined forms or checklists. However, use these documents with caution as they may be limiting in some cases. Always provide all of the information needed to help others understand the causes of the event, and why the recommendations are important.
Recommendations Should Not:
- Propose any punitive actions.
- Propose briefing unit personnel on the accident. Such briefings are basic management responsibility and a normal function of safety managers and supervisors at all organizational levels.
- Recommend that a new policy, regulation, or standard operating procedure is needed when established guidelines exist but are not followed.
PREVENTION
There are obviously situations in which workers must disturb an injury or fatality scene, including these:
- You are trying to save a worker’s life or relieve someone’s suffering following an incident.
- You are trying to prevent serious damage or loss of property following an incident.
- You are attempting to maintain access to essential services such as water, gas or electricity.
Otherwise, you should not be entering the scene unless you have authority to do so or the investigator has concluded his or her examination of the area and given permission for workers to regain access. Tampering with an accident/incident scene to make it look as though conditions were compliant with safety regulations is extremely risky, not to mention foolish. Safety investigators can interview witnesses, including victims who survive their injuries and quickly determine that you aren’t telling the truth. A lie can snowball and if you continue the deception you can be caught under a legal avalanche. Don’t become part of any cover-up if a coworker asks you to lie for him or her. You’ve got nothing to gain and everything to lose, including your job and possibly, your freedom.
If you are first on the scene of a workplace accident, help the injured person and call for emergency medical help if required. As soon as possible, contact your supervisor and report the incident. If you witnessed what happened, write down the details of what you saw and heard. Your observations will help investigators determine what happened and how to prevent a similar incident in future.
One of the biggest challenges when you are investigating an incident is sorting out the irrelevant information from the relevant information. More specifically – determine what is relevant to what happened, how it happened, and especially why it happened.
One way to do this is by using a systematic approach to investigate all incidents that focuses on finding the root causes. Doing so, means you can implement relevant and meaningful corrective actions.
You can use this 4-step approach to guide you. It can also be used as a training tool for members of your investigation team.
Step 1 – Preserve and Document the Scene
After you have verified the scene is safe and victims are being care for, the first step in the investigation is to secure the incident site to prevent evidence from being moved, altered, or tampered with.
- If evidence goes missing or is messed with – you are going to miss out on important clues on what caused the event.
- Use cones, tape, or barriers to physically block off the scene.
- You can use photos or videos to preserve and document the scene.
Document the incident facts:
- Date and time of incident
- Investigator
- Name/s of the injured
- Injury description
- Date, time, and location of incident
Step 2 – Collect Information
Collecting information of events leading up to the incident, the incident itself, and other important information is necessary to establish a timeline, identify victims and witnesses, and begin to uncover the initial and root causes of the incident.
One of the primary ways to gather information is to interview witnesses and the victim/s. The sooner a witness or victim is interviewed, the more accurate and candid his/her statement will be.
Set the interviewee at ease:
- Clearly state the purpose of the investigation and interview – to learn how to prevent future incidents and notto blame any one person.
- Interview witnesses separately – as least initially. A witness might say more if they aren’t in the same room as their supervisor, co-worker, or the victim. The same is true for when you interview the victim.
- Let employee know they have a right to have employee representative (e.g., labor representative) present, if available/appropriate.
- Conduct interviews in a quiet space, although in some cases, it might make sense to interview someone at the scene of the incident. It might help them explain something better, jog their memory, or help you both put questions and responses in context.
Now you’re ready to begin the interview.
- Ask the individual to recount their version of what happened and don’t interrupt them.
- Take notes and/or record the responses; interviewee must give permission prior to being recorded.
- Have paper and pen/pencil available for interviewee.
- Ask clarifying questions to fill in missing information; repeat back to the interviewees the information obtained; and correct any inconsistencies.
- Ask the individual what they think could have prevented the incident.
In addition to interviews, other sources of helpful information include:
- Equipment manuals
- Industry guidance documents
- Company policies and records
- Maintenance schedules, records and logs
- Training records (including communication to employees)
- Audit and follow‐up reports
- Enforcement policies and records
- Previous corrective action recommendations
Step 3 – Determine the Root Causes
The root causes are the underlying reasons why the incident occurred. Root causes generally reflect management, design, planning, organizational and/or operational failings (e.g., employees were not trained adequately; a damaged guard had not been repaired).
If you truly want to prevent a repeat of an incident, you must go beyond the easy surface causes – “worker was careless” or “employee didn’t follow the SOP.” Focusing on the easy causes is a lazy way out and it won’t get you the answers you need to put meaningful corrective actions in place.
Remember: Investigations are not effective if they are focused on finding who to blame because they will stop at the initial incident and stop short of discovering the root causes.
Step 4 – Implement Corrective Actions
Your investigation isn’t done until all the underlying causes of the incident have been identified and corrective actions are in place.
Some of the corrective actions will be quick and easy fixes; others may take more time and planning. Some may be specific and address a root cause directly and others may be sweeping improvements to the safety program in general.
Regardless, it is important that you communicate the corrective actions throughout the workplace. Employees pay attention to what management pays attention to and what management ignores. If you ignore incidents or don’t follow through on corrective actions your employees will get the message loud and clear. Employee safety isn’t valued.
So, take time to develop appropriate corrective actions and manage them through to completion.