Hazard Communication Standards – Quick Tips
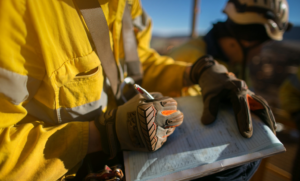
Know your standard: hazard communication ensures that employers and employees have the information they need to stay safe on the job.
Introduction
The Occupational Safety and Health Administration (OSHA) promulgated the Hazard Communication Standard on November 25, 1983 and it became effective two years later. Minor technical amendments and changes were made in 1987-1989 and 1994. On March 26, 2012, OSHA adopted portions of the Third Edition of the United Nations’ Globally Harmonized System of Classification and Labeling of Chemicals (GHS), into the Hazard Communication Standard. It was effective 60 days thereafter (May 25, 2012) and had a four-year transition period.
The revised Standard provides harmonized criteria for classifying chemicals and requires specific label elements on shipped containers and mandatory 16-section standardized safety data sheets (SDSs). Prior to this revision, information was conveyed on labels and material safety data sheets (MSDSs) in whatever formats the supplier chose. The purpose of the Hazard Communication Standard has remained the same since it was first enacted—to ensure that the hazards of all hazardous chemicals imported, produced or used in U.S. workplaces are evaluated and that the information is transmitted to affected employers and potentially exposed employees. This transfer of information is to be accomplished by means of a comprehensive hazard communication program that includes container labeling and other forms of warning, Safety Data Sheets (SDS) and employee training.
Categories of the Hazard Communication Standard
The Standard contains six major categories: Hazard Classification, Written Hazard Communication Program, Labels and other Forms of Warning, Safety Data Sheets, Employee Information and Training and Trade Secrets.
Hazard Classification
The first category, Hazard Classification (29 Code of Federal Regulations (CFR) 1910.1200 (d)) requires chemical manufacturers and importers to evaluate the chemicals produced in their workplaces or imported by them to determine the hazard classes, and, where appropriate, the category of each class. Mandatory classification considerations are given in 29 CFR 1910.1200 Appendix A (Health Hazard Criteria) and Appendix B (Physical Criteria).
Chemicals exempt from the standard include: wood and wood products (except wood dust), regulated hazardous waste, tobacco products, food, drugs, cosmetics, alcoholic beverages, agricultural or vegetable seed treated with pesticides, various types of pesticides, nuisance particulate and articles. These are exempt because they are all regulated by separate government agencies.
Written Hazard Communicating Program
The second category is the Written Hazard Communication Program (29 CFR 1910.1200(e)). It requires employers to fully document the actions taken to comply with all of the provisions of the HCS and to list the responsible person(s) for each area of the program. A copy of the written program must be made available, upon request, to all employees and OSHA officials.
Labels and other Forms of Warning
The third category, Labels and other Forms of Warning (29 CFR 1910.1200(f)), requires chemical manufacturers, importers or distributors to ensure that each container of hazardous chemicals leaving their workplace, i.e. shipped container, is labeled, tagged or marked with the following six elements:
- Product Identifier– name or number used for a hazardous chemical on a label or SDS and a unique means to identify the chemical.
- Pictogram– symbol plus other graphic elements to convey specific hazard information. There are nine pictograms under GHS. OSHA addresses eight of the nine – environmental hazards are not governed by OSHA.
- Signal Word is used to indicate the relative level of severity of hazard. DANGER is used for the more severe hazards and WARNING is used for less severe hazards.
- Hazard Statement– describes the nature and degree of the hazard(s).
- Precautionary Statement– phrase that describes recommended measures that should be taken to minimize or prevent adverse effects resulting from exposure or improper storage or handling.
- Supplier Information– name, address, and telephone number of the chemical manufacturer, importer, or other responsible party.
The signal word, hazard statement(s), and pictogram(s) must be grouped together on the shipped container label and NOT separated on the container or outside packaging.
With the revision to the Hazard Communication Standard, OSHA continued to give employers the flexibility to determine what types of workplace labels they use. Employers have the ability to choose to label workplace containers either with the same label information that the chemical manufacturer or importer used on the shipped containers or with alternate labels that meet the requirements of the standard.
Each shipped container and workplace label must be prominently displayed in English, however other languages may also be included if appropriate for your workplace.
Safety Data Sheets
The fourth category, Safety Data Sheets (SDSs) (29 CFR 1910.1200(g)) requires that chemical manufacturers, importers or distributors provide SDSs for each hazardous chemical to downstream users to communicate information on the hazards. All of the information on the SDS must be in English and be available to employees working with or near the hazardous chemical. SDSs are presented in a consistent user-friendly, 16-section format.
Sections 1 through 8 of the SDS contain general information about the chemical, identification, hazards, composition, safe handling practices, and emergency control measures. Sections 9 through 11 and 16 contain other technical and scientific information, such as physical and chemical properties, stability and reactivity information, toxicological information, exposure control information, and other information including the date of preparation or last revision. To be consistent with the required 16-section format, the SDS must also contain Sections 12 through 15 – ecological information, disposal considerations, transport information and other regulatory information. OSHA does not enforce the content of these sections because they fall outside of its’ jurisdiction. A description of all 16 sections of the SDS, along with their contents, is given below:
- Identification includes product identifier; manufacturer, importer or other responsible party name, address, phone number; emergency phone number; recommended use; restrictions on use.
- Hazard Identification includes all hazards and the appropriate warnings regarding the chemical; required label elements.
- Composition/information on ingredients includes information on chemical ingredients; trade secret claims.
- First-aid measures include important symptoms/effects acute, delayed; required treatment.
- Fire-fighting measures list suitable extinguishing techniques, equipment; chemical hazards from fire.
- Accidental release measures list emergency procedures, protective equipment; proper methods of containment and cleanup.
- Handling and storage lists precautions for safe handling and storage, including incompatibilities.
- Exposure controls/personal protection lists OSHA’s Permissible Exposure Limits (PELs); American Conference of Governmental Industrial Hygienists (ACGIH) Threshold Limit Values (TLVs); and any other exposure limit used or recommended by the chemical manufacturer, importer, or employer preparing the SDS where available as well as appropriate engineering controls; personal protective equipment (PPE).
- Physical and chemical properties list the chemical’s characteristics.
- Stability and reactivity lists chemical stability and possible hazardous reactions.
- Toxicological information includes routes of exposure; related symptoms, acute and chronic effects; numerical measures of toxicity.
- Ecological information provides ecotoxicity, persistence and degradability, bio accumulative potential, mobility in soil and other adverse effects information.
- Disposal considerations provide description of waste residues and information on their safe handling and methods of disposal, including the disposal of any contaminated packaging.
- Transport information provides guidance on classification information for shipping and transporting hazardous materials by road, air, rail or sea.
- Regulatory information provides product specific safety, health and environmental regulations.
- Other information includes the date of preparation or last revision.
Employee Information and Training
The fifth category, Employee Information and Training (29 CFR 1910.1200(h)), requires employers to provide employees with effective information and training on hazardous chemicals in their work area at the time of their initial assignment and whenever a new physical or health hazard is introduced into the area. The training must include methods and observations used to detect the presence or release of the chemical, physical and health hazards, protective measures, labeling and explanation of the SDS.
Trade Secrets
The sixth and final category involves manufacturer Trade Secrets (29 CFR 1910.1200(i)). The chemical manufacturer may withhold the chemical identity, including the chemical name and other specific information, from the SDS. If a trade secret is claimed, it must be indicated on the SDS. However, under special conditions, the substance’s proprietary information may be obtained by health care professionals immediately if a medical emergency exists or requested in a non-emergency situation. Provisions for a written statement of need and confidentiality agreement will be based on the situation circumstances.
Commonly Asked Questions
- The United Nations revises the Globally Harmonized System of Classification and Labeling of Chemicals (GHS) every two years. Did OSHA anticipate needing future updates of the Hazard Communication Standard and how is OSHA communicating these changes?
A:OSHA did anticipate that future updates of the Hazard Communication Standard may be necessary and determined that they would be done through various rulemaking options, including:
- Technical updates for minor terminology changes
- Notice and Comment rulemaking for more substantive or controversial updates such as additional criteria or changes in health or safety hazard classes or categories
- Direct Final Rules for text clarification
Q: What portions of the Hazard Communication Standard must employers who only use chemicals and do not produce or import them focus on?
A: Employers who do not produce or import chemicals need only focus on those parts of the Standard that deal with establishing a workplace program and communicating information to their workers.
Sources
29 CFR 1910.1200, Hazard Communication
United Nations’ Globally Harmonized System of Classification and Labeling of Chemicals, Revision 3
(Rev 7/2018)
The information contained in this article is intended for general information purposes only and is based on information available as of the initial date of publication. No representation is made that the information or references are complete or remain current. This article is not a substitute for review of current applicable government regulations, industry standards, or other standards specific to your business and/or activities and should not be construed as legal advice or opinion. Readers with specific questions should refer to the applicable standards or consult with an attorney.
Source: Grainger Know How – https://www.grainger.com/know-how