Guarding Elevated Locations Meeting Kit
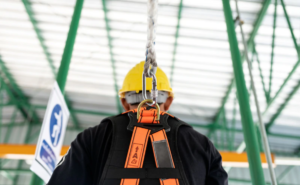
Falls are among the most common causes of serious work-related injuries and deaths. Employers must set up the work place to prevent employees from falling off of elevated work stations. Falls are among the most common causes of serious work-related injuries and deaths. Employers must set up the work place to prevent employees from falling off of overhead platforms, elevated work stations or into holes in the floor and walls.
A fall from elevation can seriously injure or kill a worker. Employers should implement a fall safety program by identifying potential fall hazards throughout the workplace, training employees, providing fall protection equipment, and placing guardrails around elevated locations. Guardrails protect workers from falls and act as a barrier to prevent tools and equipment from falling on workers below.
ELEVATE SAFETY PROGRAM
Falls from heights are a concern at many worksites and there are threshold heights established where various types of fall protection are required. For employees in general industry, the height is 4 feet above a lower level. In construction work, the threshold height is 6 feet above a lower level. Fall protection on scaffolding is required at 10 feet. In addition to falls from heights, workers also can slip or trip on ground surfaces that are uneven or cluttered with debris.
FALL PROTECTION SYSTEMS AND EQUIPMENT
The key to protecting employees is to use the right type of fall protection systems and training.
Ladders — First, fall protection is not required for portable ladder use in either general industry or construction work. You don’t want employees tying off to ladders or other objects nearby. Fixed ladders are a different story, as they may or may not have cages or ladder safety devices.
OSHA’s general industry fall protection regulations are at 29 CFR 1910.23, Guarding Floor and Wall Openings and Holes. Fall protection systems (e.g., guardrails for platforms and railings for stairs) are addressed, but personal fall arrest equipment, such as lanyards and harnesses, are not.
Housekeeping — High traffic areas should be kept free from tools, materials, debris or spilled or leaked liquids. These types of items can contribute to slips and trips on the same level. OSHA requires employers, in 1910.22(a), to keep their facilities clean, orderly, and as dry as possible.
For work on a level surface that could pose a slip hazard, you can install slip-resistant floors. Options to increase slip-resistance include materials such as textured, serrated, or punched surfaces and steel or metal grating. These types of floor surfaces often can be installed in work areas that are slippery because of wet, oily, or dirty operations. Another option is to provide slip-resistant footwear, which also may be useful in reducing slipping hazards.
Guardrails and handrails — Falls from an elevation involve falling from one level to another. Examples include falling from a scaffold to the ground below. There are several types of fall prevention systems you can use to stop a fall from an elevated surface:
A guardrail is a vertical barrier, normally consisting of an assembly of top rails, midrolls and posts, erected to prevent employees from falling to lower levels. A toe board is a barrier placed to prevent the fall of materials to a lower level, or to keep employees’ feet from slipping over an edge. Falling objects also can be hazards, especially tools dropped or kicked from scaffolds or work platforms such as scissor or aerial lifts.
Well built guardrails are a reliable and convenient means of fall protection because they act as a visible and physical barrier to help prevent falls from heights or between levels including falls from roofs, balconies, stairwells or falls into open holes. Guardrails are used where covers, floors or walls cannot be installed or are not practical.
A standard railing consists of a top rail, intermediate rail, and posts, and has a vertical height of 42 inches from the upper surface of the top rail to floor, platform, runway or ramp level. The top rail must be smooth surfaced throughout the length of the railing. There must be an intermediate railing approximately halfway between the top rail and the floor.
A standard toe board needs to be 4 inches in vertical height from its top edge to the level of the floor, platform, runway, or ramp. It has to be securely fastened in place and with not more than ¼-inch clearance above floor level. The toe board can be made of any substantial material that either is solid or has openings 1 inch or less in size.
HAZARD IDENTIFICATION AND GUARDRAILS USE – GUIDELINES
- Look for areas with high personnel traffic.
- Determine vulnerable structures.
- Assess inventory storage locations.
- Note areas with significant elevation changes.
- Identify dangerous or crucial equipment.
- Select guardrail fit for purpose.
GENERAL INDUSTRY AND CONSTRUCTION FALL PROTECTION
Sometimes fall prevention systems can’t be used. In these cases, employers need to provide personal fall arrest equipment. These systems often consist of lanyards, harnesses and anchorage devices that may not prevent the fall but reduce the chance of injury or death if the employee does fall.
Another means of fall protection includes personal fall arrest systems to stop an employee after a fall from a working level. These are widely used in the construction industry, but OSHA only specifically permits their use in general industry under the standard for powered platforms for building maintenance.
While the vast majority of systems in use now meet national consensus standards, OSHA says if a personal fall arrest system has to be used, it must consist of an anchorage, a connector, and a body harness. The arrest system also may include a lanyard, deceleration device, lifeline, or a combination of the above. As stated, OSHA only outlines general industry requirements for personal fall arrest systems under Appendix C to 1910.66, which requires that anchorages to which personal fall arrest equipment is attached be capable of supporting at least 5,000 pounds. Appendix C also states that personal fall arrest systems must bring an employee to a complete stop and limit maximum deceleration distance an employee travels to 3.5 feet. Fall protection is required at 4 feet in general industry. That’s why the required stopping distance is 3.5 feet.
FINAL WORD
Protecting employees from falls should be a concern for all employers. Always select fall protection measures and equipment compatible with the type of work being performed. Fall protection generally can be provided through the use of proper housekeeping, guardrails and handrails, safety nets, personal fall arrest equipment, positioning devices and warning line systems.