Fume Removal – Quick Tips
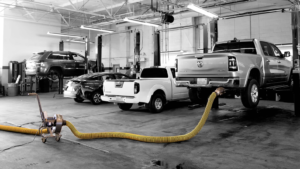
A fume hood or fume removal system is a device used to capture hazardous chemical vapors, gases, dusts, mists and metal fumes in a work process. These systems help eliminate or lower human exposure to hazardous fumes. A fundamental safety and industrial hygiene principle is to control exposure to hazards with engineering and administrative controls before implementing personal protective equipment. OSHA states this in the Respiratory Protection Standard, 29 CFR 1910.134.
Fume hoods represent an engineering control used to help reduce exposure to hazardous substances. A fume removal system consists of at least two of the following components: collection hood, ducting, air cleaning device and blower.
Regulations
There are government regulations and industry standards that either directly or indirectly require the use of fume removal equipment. This section will identify and highlight many of those regulations.
The Air Contaminant Standard, Title 29 of the Code of Federal Regulations (CFR) Part 1910.1000, established Permissible Exposure Limits (PEL) for many common industrial and laboratory chemicals. A PEL is the highest average chemical concentration that workers can be exposed to in an eight-hour work day and forty-hour work week. There are also substance-specific standards for Asbestos: 29 CFR 1910.1001, Cadmium: 29 CFR 1910.1027, Formaldehyde: 29 CFR 1910.1048, Benzene: 29 CFR 1910.1028, Lead: 29 CFR 1910.1025, and others, which identify the PEL and other regulations for each contaminant.
The Occupational Exposure to Hazardous Chemicals in the Laboratory Standard, Part 29 CFR 1910.1450, mandates that employers control employee chemical exposure below established PEL through the implementation of a chemical hygiene plan. Chemical hygiene plans are developed by employers for their specific facilities and applications. Statements outlining the use of fume removal equipment and maintenance of the equipment are included in this plan.
The American National Standards Institute (ANSI) has several industry conformance standards that impact fume removal equipment. The ANSI Z9.5-2003 Laboratory Ventilation Standard deals specifically with the design and operation of laboratory ventilation systems. ANSI Z9.2-2006, Fundamentals Governing the Design and Operation of Local Exhaust Systems, deals specifically with industrial ventilation and fume removal applications. These two ANSI standards are referenced in 29 CFR 1910.94 Ventilation Standard.
In addition to these regulations, local building codes, fire codes and environmental regulations all need to be investigated prior to system design and installation.
Components of a Fume Removal System
A fume removal system will consist of two or more of the following components: A blower, ducting, air cleaning device and collection hood.
The blower is a major component of every system and must be selected carefully. Blowers need to be sized properly in order to effectively remove the contaminant from the work area. Blowers are sized and rated by the amount of air, measured in cubic feet per minute, that can move at a given amount of resistance. The resistance is known as static pressure and is measured in inches of water. It is the amount of resistance the fan must overcome in order to move air through the ventilation system. The amount of static pressure in a system is influenced by the type of collection device, length of ducting, number and amount of turns in the ducting and type of air purification device (if used). Consult a ventilation specialist to determine the correct blower size for each particular application.
Blower flywheels are available in a variety of materials (steel, aluminum, plastic) for different applications. Non-sparking flywheels should be chosen when working with flammable materials. Explosion-proof blowers are available for locations that could be potentially explosive. The motors on these blowers help reduce the possibility of explosion in certain types of environments.
Ducting is the material through which the air and contaminants are moved. Common materials are galvanized steel, stainless steel, PVC and other rigid or flexible plastic materials. Angles for fitting corners and reducers for connecting different size ducts are all available accessories.
Air purification devices will either be mechanical filters or chemical adsorption media. Mechanical filters are used to remove particulate contaminants. The type of filter selected will be determined by the application and particle size of the contaminant. HEPA filters are the most efficient type available and can filter particles of 0.3 microns in size. Mechanical filters will gradually become plugged with the particulate material and air flow will decrease. Pressure gauges and air flow indicators can help determine when filters need to be changed.
The use of air purification devices prior to exhausting air outside your facility may be required by your local Environmental Protection Agency (EPA). Determine this prior to designing a system. Cleaning the air and then exhausting it back into the work environment is normally not a recommended practice. However, it can be done if the contaminant concentrations generated are below the PEL and the chemical has good warning properties.
Activated carbon is one type of chemical sorbent that can be used for many organic vapors. Other absorption materials are available, depending on the chemical and application. Absorption filters need to be changed when they become full. Chemical concentration, humidity, air flow and the chemical’s physical properties all play a role in the life of a chemical absorption filter. Warning properties of the contaminant can indicate when to change the filter. A safer way to monitor the exhaust air is to test for chemical breakthrough on a routine basis.
The type of collection device used in a fume removal system will depend on the application, the physical properties of the contaminant and the work environment. Three primary types of collection devices are: Cabinet hoods with vertical or horizontal sashes, canopy hoods and local collection hoods which attach directly to a length of ducting.
Cabinet hoods are often used in lab applications because they are effective for a variety of chemical contaminants. The three-sided enclosure is usually made of a chemically resistant material. A horizontal or vertical sash will control air flow through the front opening and can be positioned to offer the best chemical containment. Air is pulled through the front opening and away from the worker. Proper blower size and sash height help reduce the chance of turbulence within the hood, which could allow the contaminant to escape. Air currents from the mechanical ventilation system and traffic moving by the hood can all affect the ability of the cabinet to contain and remove the contaminant being generated.
Canopy hoods are wall-mounted or hung from the ceiling over the work process and may or may not have side panels. This type of hood works best in applications where the contaminant rises and the worker is not directly under the hood. Cross drafts decrease the effectiveness of these hoods, although side panels can minimize these effects.
Local collection hoods attach directly to a length of ducting. Hood shape varies depending on the application and the air flow needed to capture the contaminant. These devices are designed for applications where the contaminant is generated at a localized point. Proper positioning of these hoods is critical to their effectiveness.
Definitions
Anemometer—A device that measures air velocity, usually in feet per minute.
Bypass fume hood—A cabinet fume hood constructed so that as the sash closes, air is allowed to bypass the hood face through another opening, usually above the sash. This bypass provides a constant face velocity and hood static pressure.
Capture velocity—The velocity of air induced by a hood to capture emitted contaminants external to the hood.
Ductless fume hood—A fume removal system that uses an air purification device and returns exhaust air to the indoor environment.
Dilution ventilation—A form of exposure control that relies on the dilution of airborne contaminants in the workplace air.
Fan curve—A curve relating pressure versus volume flow rate of a given fan at a fixed speed (rpm).
Local exhaust ventilation—A ventilation system that captures and removes emitted contaminants before dilution into the workplace ambient air can occur.
Manometer—A device that measures pressure difference, usually in inches of water gauge.
Static pressure—The pressure developed in a duct by a fan.
Sources
29 CFR 1910.1000, Air Contaminant Standard
29 CFR 1910.1001, Asbestos Standard
29 CFR 1910.1027, Cadmium Standard
29 CFR 1910.1048, Formaldehyde Standard
29 CFR 1910.1028, Benzene Standard
29 CFR 1910.1025, Lead Standard
29 CFR 1910.1450, Occupational Exposure to Hazardous Chemicals in the Laboratory Standard
29 CFR 1910.94, Ventilation Standard
American National Standards Institute (ANSI)
ANSI Z9.5-2003, Laboratory Ventilation Standard
ANSI Z9.2-2006, Fundamentals Governing the Design and Operation of Local Exhaust Systems
Environmental Protection Agency (EPA)
The information contained in this article is intended for general information purposes only and is based on information available as of the initial date of publication. No representation is made that the information or references are complete or remain current. This article is not a substitute for review of current applicable government regulations, industry standards, or other standards specific to your business and/or activities and should not be construed as legal advice or opinion. Readers with specific questions should refer to the applicable standards or consult with an attorney.
Source: Grainger Know How – https://www.grainger.com/know-how