Faceshield Protection – Quick Tips
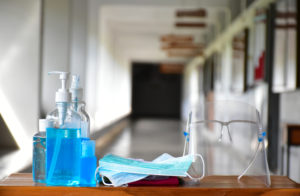
Faceshield protection is an important part of personal protective equipment (PPE). Employers are recognizing the added protection that faceshields provide and usage is growing.
Eye and Face Protection Criteria
The Occupational Safety and Health Administration’s (OSHA’s) regulation 29 CFR 1910.133 requires the use of eye and face protection when workers are exposed to eye or face hazards such as flying objects, molten metal, liquid chemicals, acids or caustic liquids, chemical gases or vapors, or potentially injurious light radiation.
The original OSHA standards addressing eye and face protection were adopted in 1971 from established Federal standards and national consensus standards. Since then, OSHA has amended its eye and face protection standards on numerous occasions.
The American National Standards Institute (ANSI) American National Standard for Occupational and Educational Personal Eye and Face Protection Devices standard Z87.1 was first published in 1968 and revised in 1979, 1989, 2003, 2010 and 2015. The 1989 version emphasized performance requirements to encourage and accommodate advancements in design, materials, technologies and product performance. The 2003 version added an enhanced user selection chart with a system for selecting equipment, such as spectacles, goggles and faceshields that adequately protect from a particular hazard. The 2010 version focused on a hazard, such as droplet and splash, impact, optical radiation, dust, fine dust and mist, and specifies the type of equipment needed to protect from that hazard. The 2015 revision continues to focus on product performance and harmonization with global standards. The 2015 standards fine-tune the 2010 hazard-based product performance structure.
The majority of eye and face protection in use today is designed, tested and manufactured in accordance with the ANSI Z87.1-2010 standard. It defines a faceshield as “a protector commonly intended to, when used in conjunction with spectacles and/or goggles, shield the wearer’s face, or portions thereof, in addition to the eyes from certain hazards, depending on faceshield type.”
ANSI Z87.1-2015 defines a faceshield as “a protector intended to shield the wearer’s face, or portions thereof from certain hazards, as indicated by the faceshield’s markings.” A protector is a complete device—a product with all of its components in their configuration of intended use.
Although it would seem that from the faceshield definition change from 2010 to 2015 that faceshields meeting the performance criteria of the 2015 standard can be used as standalone devices, all references in the modified Eye and Face Protection Selection Tool refer to “faceshields worn over goggles or spectacles.”
Faceshield Selection
When selecting faceshields, it is important to understand the importance of comfort, fit and ease of use. Faceshields should fit snugly and the primary way to ensure a snug fit is through the headgear (suspension). Headgear is usually adjustable for circumference and depth. The headband is adjusted for circumference fit and the top band is adjusted for depth. When worn properly, the faceshield should be centered for optimal balance and the suspension should sit between half an inch and one inch above the eyebrows. Since faceshields are used in conjunction with other PPE, the interaction among the PPE needs to be seamless. Simple, easy-to-use faceshields that allow users to quickly adjust the fit are best.
Faceshield Visor Materials
Faceshield visors are constructed from several types of materials. These materials include polycarbonate, propionate, acetate, polyethylene terephthalate glycol (PETG) and steel or nylon mesh. It is important to select the proper visor for the work environment.
Polycarbonate material provides the best impact and heat resistance of all visor materials. Polycarbonate also provides chemical splash protection and holds up well in extremely cold temperatures. Polycarbonate is generally more expensive than other visor materials.
Acetate provides the best clarity of all the visor materials and tends to be more scratch resistant. It also offers chemical splash protection and may be rated for impact protection.
Propionate material provides better impact protection than acetate while also offering chemical splash protection. Propionate material tends to be a lower price point than both acetate and polycarbonate.
Polyethylene terephthalate glycol (PETG) offers chemical splash protection and may provide impact protection. PETG tends to be the most economical option for faceshield choices.
Steel or nylon mesh visors provide good airflow for worker comfort and are typically used in the logging and landscaping industry to help protect the face from flying debris when cutting wood or shrubbery.
Specialty Faceshield Protection
Arc Flash – These faceshields are used for protection against an arc flash. The requirements for arc flash protection are given in the National Fire Protection Association (NFPA) 70E standard. Faceshields are included in this standard and must provide protection based on an Arc Thermal Performance Value (ATPV), which is measured in calories per square centimeter (cal/cm2). The calorie rating must be determined first in order to select the shield that will provide the best protection. Refer to Quick Tips #263 NFPA 70E: Electrical Safety Summary for more information on the proper selection of PPE.
Heat and Radiation – There are faceshields that provide protection against heat and radiation. These faceshields prevent burns by filtering out intense ultraviolet (UV) and infrared (IR) radiation. They are made from polycarbonate with special coatings. An example of this would be adding a thin layer of gold film to increase reflectivity.
Welding – Shaded welding faceshields provide protection from UV and IR radiation generated when working with molten metal. The shades usually range from Shade 2 to14, with Shade 14 being the darkest shade. Refer to Quick Tips #109: Welding Safety for more information on selecting the proper welding faceshields.
PPE Hazard Assessment, Selection and Training
When selecting a faceshield or any other PPE, OSHA suggests conducting a worksite hazard assessment. OSHA provides guidelines in 29 CFR 1910 Subpart I Appendix B on how to evaluate worksite hazards and how to select the proper PPE. After selecting the proper PPE, employers must provide training to workers on the correct use and maintenance of their PPE. Proper hazard assessment, PPE selection and training can significantly reduce worker injuries and help to ensure a safe work environment.
Frequently Asked Questions
Q: What is the best faceshield visor for a specified chemical?
A: OSHA suggests that PPE such as faceshield protection should be used as a last resort, as an engineering solution is preferred when working with potentially injurious chemicals. Engineering solution examples include using a chemical splash guard or a fume hood. A chemical splash guard or a fume hood will stop injurious chemicals from ever reaching the face. If an engineering solution is not practical, a faceshield will offer limited chemical splash protection. The manufacturer of the faceshield is the best source for chemical-resistance data.
Q: Can I use an inexpensive faceshield for impact protection?
A: Both ANSI Z87.1-2010 and ANSI Z87.1-2015 categorize faceshields as either impact or non-impact. ANSI Z87.1-2010 and 2015 rated faceshields with a “+” symbol stamped on the faceshield (meaning impact rated) provide impact protection regardless of price. Manufacturer testing of visor materials indicate that polycarbonate offers the best impact protection and PETG offers the least. With this said, visors made from both polycarbonate and PETG may meet the ANSI testing standards for impact, even though polycarbonate is generally the most expensive visor material. OSHA states that “the employer must provide PPE to workers that give sufficient protection from the hazard”. Polycarbonate would be a better choice if the hazard requires a higher impact protection than PETG.
Sources
ANSI Z87.1 – 2015, 2010, 2003 and 1989(R-1968)
Quick Tips #109: Welding Safety
Quick Tips #263: NFPA 70E: Electrical Safety Summary
http://www.plasticsintl.com/datasheets/PETG.pdf
The information contained in this article is intended for general information purposes only and is based on information available as of the initial date of publication. No representation is made that the information or references are complete or remain current. This article is not a substitute for review of current applicable government regulations, industry standards, or other standards specific to your business and/or activities and should not be construed as legal advice or opinion. Readers with specific questions should refer to the applicable standards or consult with an attorney.
Source: Grainger Know How – https://www.grainger.com/know-how