Construction Safety Training Programs in 6 Steps
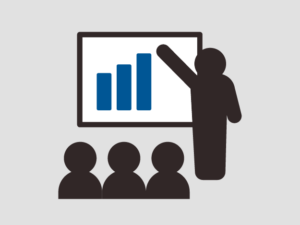
A critical element of every construction company’s environmental health and safety (EHS) program, and one that company executives expect from their EHS managers, is the development and delivery of training courses.
A critical element of every construction company’s environmental health and safety (EHS) program, and one that company executives expect from their EHS managers, is the development and delivery of training courses. Meeting this expectation in today’s resource-constrained, outsourced world is a challenge for even the most proficient of EHS professionals. It’s especially daunting for construction training coordinators whose responsibilities are not limited to the realm of EHS. This article outlines six steps to help you implement a new training program or jump start an existing one.
The Significance of a Near Miss
Safety directors, supervisors and others in charge of creating and implementing the company’s safety program do their best to prevent illness and injury. But good intentions and earnest effort aren’t enough. All of us make mistakes. There’s no such thing as a perfect human being. The corollary to this principle is that there’s no such thing as a perfect safety program.
The second corollary is that every safety program has some flaw somewhere. The important thing is to figure out where the flaws are and fix them. The crucial question: Will you discover the flaws in your own program before somebody gets hurt? Or will it take injury or illness to bring them to light?
The answer to that question depends in large part to how you respond to close calls.
Not all incidents injure people and damage property. Close calls are the incidents where nobody or nothing gets hurt. It could be anything from someone walking in an aisle and almost getting hit by an opening door to a screwdriver being dropped to the floor by the maintenance guy working on a ladder and narrowly missing the skull of a maintenance worker below. A close call is thus a “free shot” to identify and fix problems in a safety program before they do actual harm.
Why We Don’t Take Advantage of Near Misses
Close calls happen all the time. Unfortunately, companies don’t always use them to identify and fix the flaws in their safety program. Why not? The problem is that close calls are the Rodney Dangerfield of the safety world. “They get no respect.”
One of the reasons for this lack of respect is the tendency to confuse compliance for safety. For example, OSHA/OHS recordkeeping regulations require us to record and report all occupational injuries and illnesses in the workplace. But the recordkeeping requirements don’t cover close calls. And if we don’t have to report those close calls that we see happen everywhere, we tend not to pay them any attention. No harm, no foul.
So let’s say a worker almost gets hit by a falling box. The safety director might take the following view: “Wow, that was a close one! Thankfully, there was no injury, no first aid, no lost or restricted time. I almost had a boatload of paperwork, investigation, corrective action and training to do on that one.”
Respect the Close Call
Of course, that is a terrible mistake. Neglect of close calls is a missed opportunity for prevention and a recipe for future accidents. The fact that nobody got hurt or no machinery got damaged was an accident. What’s important to realize is that something went wrong and it could go wrong again. So you need to fix the problem because the next time you might not be so lucky. And you need to be grateful the close call happened because it gave you the chance to prevent an injury.
Take Action to Prevent Future Incidents
You may say that there’s no way to address close calls since you don’t know when they occur. After all, you can’t be everywhere to see them happen. And you can’t necessarily count on workers to report them.
Not knowing about close calls is a real problem. It would be naive to believe that all of the close calls that happen on the shop floor will get recognized and reported. But there are steps you can take to make it more likely for close calls to get reported. Establishing a safety conscious attitude throughout the company and explaining the importance of close calls will go a long way toward getting people on the floor to recognize and report them.
Of course, that’s easier said than done and that for many of us this may be the biggest challenge in establishing an effective safety program. This is especially true if your plant has that sports locker room code of “what happens in the shop stays in the shop.” But this is where the safety director and supervisors can really make a difference. You can change that mentality. So there’s your challenge: Go out and create that work environment atmosphere that has workers thinking safety every day, be visible, accessible, active and relentless; listen to your workers and use everyone as a resource.
Conclusion
The next time you get a call from one of your supervisors, foremen, lead persons or operators on the shop floor asking you to come and look at a potential problem, don’t think – great, here comes a load of $*#^$%#@!! paperwork. Instead, think– hey, my safety program is working. They’re telling me about a problem and giving me a chance to fix it before it does real damage. If they’re doing something right, I must be doing something right. And, if we’re all doing something right, we must be on our way to a safer and healthier workplace.