Avoid Silicosis from Abrasive Sandblasting – Quick Tips
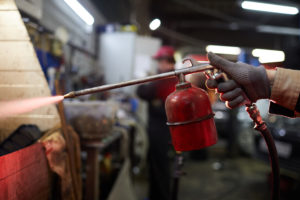
Abrasive blasting uses compressed air or water to direct a high velocity stream of an abrasive material to clean an object or surface, remove burrs, apply a texture or prepare a surface for painting. Abrasive blasting is more commonly known as sandblasting since silica sand is commonly used as the abrasive, although not the only one always used. Industries that rely on sandblasting on a daily basis include painters who work on large structures like bridges, granite monument makers, foundries and shipbuilders.
The term “silica” broadly refers to the mineral compound silicon dioxide (SiO2). Although silica can be crystalline or amorphous in form, crystalline silica is more hazardous to employees. It is most commonly found in the form of quartz, but it is also found in substances such as cristobalite, tridymite and tripoli. Breathing crystalline silica dust poses an industrial hazard and can lead to severe health problems and even death.
Exposure to silica or crystalline silica can cause silicosis and a host of other illnesses. Silicosis is one of the world’s oldest known occupational diseases, with reports of employees contracting the disease dating back to ancient Greece.
In March, 2016 the Occupational Safety and Health Administration (OSHA) issued a final rule to control exposure to respirable crystalline silica. The rule is comprised of two standards: one for Construction (29 Code of Federal Regulations (CFR) 1926.1153) and the other for General Industry (29 CFR 1910.1053) and Maritime (29 CFR 1915.1053). The Maritime and General Industry standards are exactly the same but differ from the Construction standard. The key difference lies in qualifying the worker exposure level to crystalline silica. The General Industry/Maritime Standard requires the employer to perform air monitoring to determine the eight-hour average exposure level for each affected job task. Employers governed by the Construction standard can either use a control method spelled out for common construction work tasks or perform air monitoring as detailed in the General Industry/Maritime standard.
Air Monitoring
When using silica in the workplace, the first action that needs to be completed is to see what, if any, protective measures need to be taken. To make this determination, collecting and measuring the concentration of silica in the air will need to be done. Once collected, the sample is sent to a laboratory for analysis. The results of this analysis will determine if better ventilation and/or a change in work practices or respiratory protection is needed. Typically, air monitoring is done by an Industrial Hygienist. If there is not an Industrial Hygienist or safety professional available on your worksite, contact Grainger for assistance. Grainger provides several safety based services such as collecting silica exposure samples.
The new action limit and permissible exposure limit (PEL) for crystalline silica for General Industry, Construction and Maritime are all the same and can be found in Construction (29 CFR 1926.1153), General Industry (29 CFR 1910.1053) or Maritime (29 CFR 1915.1053). The action limit is established at 25 micrograms per meter cubed (ug/m3) and the PEL is established at 50 ug/m3.
To help control the risk of respirable crystalline silica exposure, OSHA’s “three lines of defense” philosophy is suggested. The first line of defense is to eliminate and/or engineer the crystalline silica exposure hazard out. When engineering/elimination controls are not feasible or practical, the second and third lines of defense can be used to help control the crystalline silica exposure hazard. The second line of defense is administrative controls, and the last line of defense to be considered is personal protective equipment (PPE).
Three Lines of Defense
- Engineering Controls
- Substitution
- Isolation and Containment
- Ventilation
- Silica Substitutes>
OSHA suggests the first engineering control to consider is substitution. OSHA suggests using a less toxic abrasive blasting media that can be delivered with water to reduce dust generation. Some of the possible substitutes are:
- Dry ice
- Plastic bead media
- Sponge
- Sodium bicarbonate (baking soda)
- Ground walnut shells
- Ground corn cob
- High pressure water
The advantages of using a silica substitute outweigh using silica in abrasive sandblasting. Any health issues and healthcare costs related to silica would be greatly reduced or eliminated. The time and cost of implementing and maintaining engineering controls would also be eliminated. The disadvantages are that the substitutes may not be as hard as a silica product; therefore, more of the substitute may need to be used to achieve the same result. It may also be more expensive. However, with several substitute types available, there should be one product that will get your needed job done.
- Isolation and Containment
OSHA suggests if substitution is not feasible then isolation and containment is the next best engineering control method for controlling silica exposure in the workplace. Some examples of isolation and containment include:
- Use of barriers and curtain walls to isolate the blasting operation from the operator
- Use blast rooms or blast cabinets for smaller operations
- Use restricted areas for non-enclosed blasting operations
- Keep coworkers away from the blaster
A blasting room is an enclosed room where the operator works inside the area, moving around freely with respiratory protection equipment such as an accepted blasting helmet supplied air system. Sandblasting in a blasting room ( Figure 1 below), is generally performed where larger pieces need to be sand blasted. Cabinet sandblasting (Figure 2 below), another common application, is generally performed in an enclosed cabinet where the operator stands outside the cabinet and operates a sand blast nozzle through openings in the cabinet wall. Gloves usually extend into the cabinet and the silica dust is evacuated to a dust collection and ventilation system. Where a room or cabinet enclosure is not feasible, due to size or logistics, abrasive sandblasting is done in an outdoor location. The ventilation needed is dependent on each situation. OSHA standard 1910.94 (a)(4)(i) gives the requirements on the construction, installation and inspection requirements for abrasive blasting ventilation as set forth by the American National Standard Institute (ANSI) which is specified by OSHA.
Fig.2
- Ventilation
The next line of engineering controls OSHA suggests to use is ventilation. OSHA regulation 1910.94(a)(1)(viii) requires mechanical ventilation for the removal of contaminated air where abrasive sandblasting and silica use takes place. In protecting employees from contaminated air, engineering controls such as ventilation should be the first choice, after sourcing silica substitutes. This can be accomplished through a number of options. OSHA describes a ventilation system in 1910.94(a)(1)(viii) as “A system for removing contaminated air from a space, comprising two or more of the following elements (a) enclosure or hood, (b) duct work, (c) dust collecting equipment, (d) exhauster and (e) discharge stack.”
- Administrative Controls
If all engineering controls prove to be infeasible then administrative controls can be used. Perform routine cleanup using wet methods or high efficiency particulate air/absolute (HEPA) filtered vacuuming to minimize the accumulation of toxic dusts. Other suggested activities to consider include:
- Do not use compressed air to clean as this will create dust in the air
- Clean and decontaminate tarps and other equipment on the worksite
- Schedule blasting when the least number of workers are at the site
- Avoid blasting in windy conditions to prevent the spread of any hazardous materials
Personal Hygiene Practices
- Prohibit eating, drinking or using tobacco products in blasting areas
- Provide wash stations so workers can wash their hands and face routinely and before eating, drinking or smoking
- Vacuum or remove contaminated work clothes before eating, drinking or smoking
- Provide accommodations for end-of-shift showers and change areas with separate storage facilities for street clothes, protective clothing and equipment
- Keep contaminated clothing and equipment out of the clean change area
- Personal Protective Equipment (PPE) Controls
The last line of defense controls to be used when all engineering and administrative controls prove to be infeasible is PPE.
Respiratory Protection
An abrasive-blasting respirator must cover the wearer’s head, neck and shoulders to protect the wearer from rebounding abrasive. Workers must use only respirators approved by the National Institute for Occupational Safety and Health (NIOSH) to provide protection from dusts produced during abrasive-blasting operations:
- Type CE NIOSH-certified blasting airline respirator with positive pressure blasting helmet
Air purifying respirators and powered air purifying respirators (PAPR’s) are not recommended for abrasive blasting operations but they may be suitable for auxiliary work, such as clean-up operations. In very limited situations, the 1910.94(a)(5)(ii)(b) interpretation only provides for limited deviation, such as a breakdown in the air supply or when the abrasive blasting respirator is temporarily unavailable. Only then can a dust filter respirator can be used as interim protection. If it does not provide additional face and eye protection supplementary equipment will be needed. This is in accordance with the OSHA standard 1910.94 (a)(5)(v)(b).
Other Personal Protective Equipment
Whether it be General Industry 29 CFR1910, Construction 29 CFR 1926 or Shipyard 29 CFR 1915 standards, all these OSHA standards have PPE requirements that need to be followed. The requirements may also intertwine with each other such as the shipyard PPE standard 1915 referring to the 1910 standard for respiratory protection. All three industry standards are similar in their PPE requirements. The following is an example of the requirements from the shipbuilding 1915 standard for PPE.
Workers performing abrasive blasting should wear:
- A protective helmet (if the respirator design does not provide this protection and there is potential for head injury); (155)
- Appropriate protective clothing, including gloves to protect from the impact of abrasives; (34(c)(3)(iv))
- Safety shoes or boots; (156)
- Hearing protectors to reduce noise levels below the OSHA PELs; (95)
An example of typical PPE worn by a worker when performing abrasive blasting is shown in Figure 3.
Conclusion
Abrasive blasting can create a host of safety issues, considerations and necessary protections when it comes to employees in any industry in which it is performed. To help keep employees who are performing abrasive blasting and those in the areas around them safe, follow the suggestions found in OSHA’s fact sheet on protecting workers from the hazards of abrasive blasting materials.
For more on silica exposure and silicosis see our Crystalline Silicon Exposure.
Sources for Information:
Occupational Safety and Health Administration(OSHA) Fact Sheet 3697, “Protecting Workers from Hazards of Abrasive Blasting Materials”, November 2013
Occupational Safety and Health Administration(OSHA) Guidance Document, “Abrasive Blasting Hazards in Shipyard Employment”. December 2006.
The information contained in this article is intended for general information purposes only and is based on information available as of the initial date of publication. No representation is made that the information or references are complete or remain current. This article is not a substitute for review of current applicable government regulations, industry standards, or other standards specific to your business and/or activities and should not be construed as legal advice or opinion. Readers with specific questions should refer to the applicable standards or consult with an attorney.
Source: Grainger Know How – https://www.grainger.com/know-how